In the world of composite manufacturing, the spray-up method stands as a game-changing technique. Known for its efficiency, flexibility, and affordability, spray-up offers manufacturers the ability to produce high-quality fiber-reinforced polymer (FRP) composites for a wide range of applications. From creating robust marine components to lightweight automotive parts, spray-up has become an essential process in modern composite production.
This article highlights the top five reasons why the spray-up method continues to revolutionize the composite industry and why it might be the perfect choice for your next project.

1. Cost-Effective Production
One of the greatest strengths of the spray-up method is its cost-effectiveness, making it a preferred choice for businesses seeking high-quality results without incurring exorbitant expenses. Unlike other composite manufacturing processes, spray-up requires relatively low investment in tooling and equipment.
Why It’s a Smart Choice:
- Affordable Tooling: The use of open molds reduces tooling costs significantly compared to closed-mold methods.
- Material Efficiency: With precise control over resin and fiber application, material waste is minimized, reducing overall production costs.
- Scalability: Spray-up is equally suitable for small-batch projects and larger production runs, offering flexibility without excessive cost increases.
For companies looking to optimize their budgets while maintaining product quality, spray-up delivers a strong return on investment.
2. Unparalleled Design Versatility
The spray-up method excels in its ability to handle intricate designs, large components, and irregular shapes, making it an incredibly versatile process. This flexibility has made it a favorite in industries requiring custom or unique components.
How It Meets Diverse Needs:
- Complex Shapes: From curved boat hulls to decorative architectural elements, spray-up can accommodate intricate designs with ease.
- Material Customization: Manufacturers can tailor composites with specific resin types (polyester, epoxy, vinyl ester) and additives (UV inhibitors, fire retardants) to meet unique project requirements.
- Adaptability: Whether the goal is lightweight automotive parts or durable industrial components, spray-up can produce a wide variety of products.
This adaptability makes spray-up a one-stop solution for manufacturers serving diverse industries, including marine, construction, and transportation.
3. Fast and Efficient Production
In industries where time is critical, the spray-up process delivers unparalleled efficiency. Its ability to produce quality composites in shorter timeframes is one of the key reasons manufacturers turn to this method.
Efficiency in Action:
- Rapid Application: The use of a spray gun ensures quick and uniform application of resin and fibers, speeding up the production process.
- Streamlined Layering: Operators can build up composite layers to the desired thickness in a matter of minutes, reducing overall production time.
- Simultaneous Tasks: While one layer cures, new molds can be prepped, allowing for seamless workflow and increased throughput.
For manufacturers balancing tight deadlines and high-quality standards, spray-up offers the perfect blend of speed and precision.
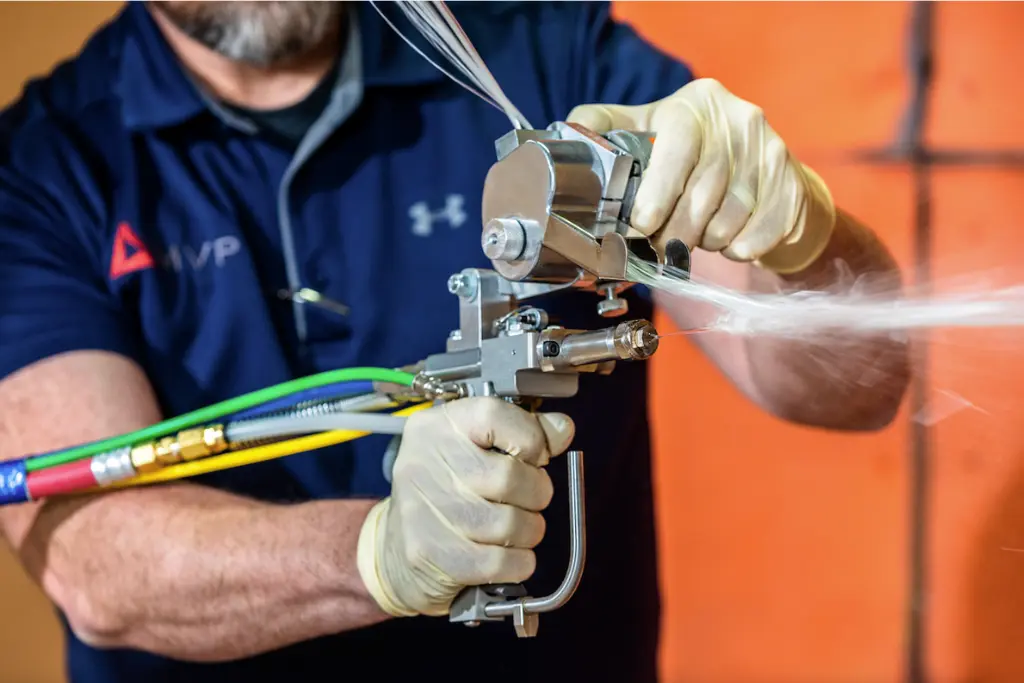
4. Durable and High-Performance Results
Products made using the spray-up method are renowned for their durability and reliability. By combining resin and fiberglass, spray-up composites achieve the perfect balance between lightweight properties and strength, making them ideal for demanding applications.
Performance Highlights:
- Strength-to-Weight Superiority: Spray-up composites are stronger than traditional materials like steel on a pound-for-pound basis, reducing material costs and transportation challenges.
- Corrosion Resistance: These composites withstand harsh environments, including exposure to moisture, chemicals, and UV radiation, making them perfect for marine, industrial, and outdoor applications.
- Long Lifespan: Thanks to their robust construction, spray-up composites require less maintenance and fewer replacements, offering long-term savings.
Whether you’re building a boat deck or an industrial tank, spray-up composites deliver the performance needed to withstand the elements.
5. Eco-Friendly Manufacturing
As sustainability becomes a key focus across industries, spray-up stands out as an environmentally friendly composite production method. Its efficiency and low waste make it a greener alternative compared to many traditional manufacturing techniques.
Why It’s Eco-Conscious:
- Low Waste: Precise application minimizes excess material, reducing overall waste during production.
- Sustainable Materials: Spray-up can incorporate eco-friendly resins and fibers to meet sustainability goals.
- Energy Efficiency: The process requires minimal energy, especially compared to more complex closed-mold systems.
For manufacturers committed to reducing their carbon footprint, spray-up offers a sustainable pathway to high-quality composites without compromising performance.
Applications of Spray-Up in Modern Industries
The versatility of spray-up has cemented its role in producing composite components for a wide range of industries:
- Marine: Spray-up is used for boat hulls, decks, and other marine structures, offering unmatched durability and water resistance.
- Construction: Architectural panels, decorative columns, and lightweight cladding benefit from the method’s design flexibility.
- Automotive: From interior panels to lightweight exterior parts, spray-up enhances vehicle performance and efficiency.
- Industrial Equipment: Chemical storage tanks, ducts, and machinery components are made with the method for superior corrosion resistance.
- Recreation: Spray-up produces water slides, playground equipment, and other recreational structures, combining durability with custom aesthetics.
Each application demonstrates the spray-up method’s ability to deliver tailored solutions for specific needs.

Innovations in Spray-Up Technology
The spray-up process continues to evolve, with advancements that enhance its efficiency, safety, and product quality. Modern innovations include:
- Automated Systems: Automated spray-up equipment ensures consistency, reduces labor costs, and minimizes errors in resin and fiber distribution.
- Low-Styrene Resins: New resin formulations reduce emissions, creating a safer work environment and aligning with environmental regulations.
- Advanced Choppers and Applicators: Improved tools ensure even fiber dispersion, resulting in composites with greater structural integrity.
These innovations ensure that spray-up remains a relevant and competitive option in the ever-evolving composite manufacturing landscape.
Why Choose Spray-Up for Your Next Project?
The spray-up method combines affordability, efficiency, and versatility, making it an unbeatable choice for composite production. Its ability to produce lightweight, durable, and corrosion-resistant products has earned it a lasting place in industries like marine, construction, and automotive.
Whether you’re creating custom components or scaling up production, spray-up delivers the results you need with the speed and flexibility you want. As advancements continue to enhance the process, spray-up remains a forward-thinking solution that meets the demands of modern manufacturing.
If you’re looking to leverage the spray-up method for high-quality composite production, explore The Front’s innovative solutions. With expertise in cutting-edge manufacturing processes, The Front delivers superior composite products tailored to meet your specific needs. Contact The Front today to see how they can bring your vision to life.