Light Resin Transfer Molding (Light RTM) is an advanced closed-mold manufacturing process used to produce high-quality fiber-reinforced polymer (FRP) composites. This method has gained popularity across various industries due to its efficiency, cost-effectiveness, and ability to produce complex, durable components with excellent surface finishes.
Understanding Light RTM
Light RTM involves placing dry fiber reinforcements, such as fiberglass or carbon fiber, into a base mold (the “A” side). A semi-rigid counter mold (the “B” side) is then positioned over the base mold, and the assembly is sealed using vacuum pressure. Catalyzed resin is introduced into the mold cavity under vacuum, ensuring thorough impregnation of the fiber reinforcements. Once the resin cures, the counter mold is removed, and the finished composite part is demolded.
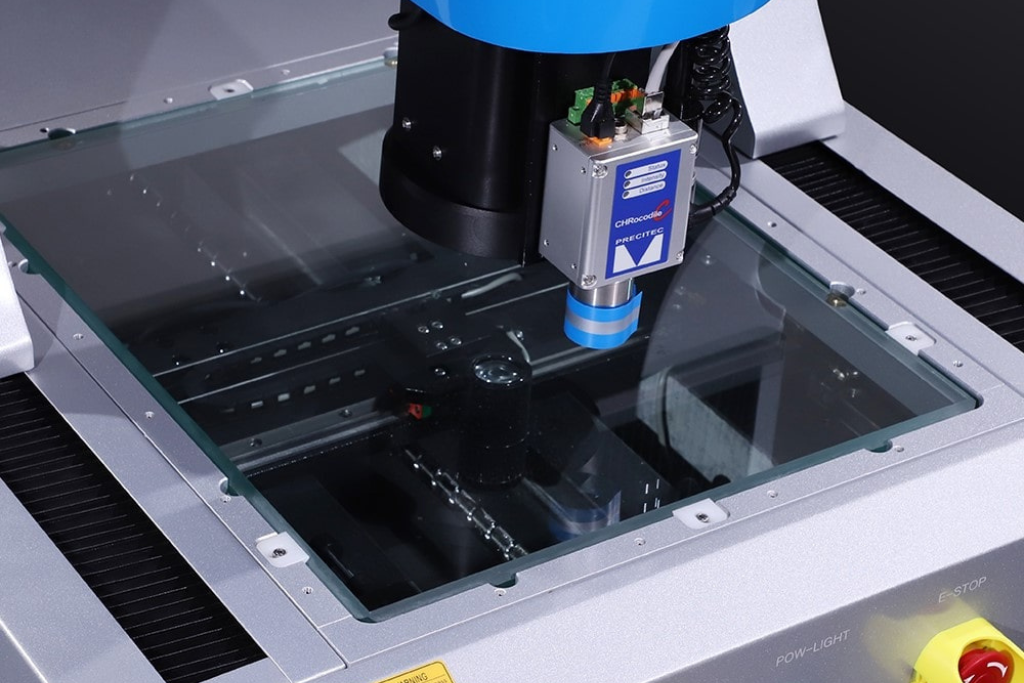
Key Advantages of Light RTM
- Cost-Effective Tooling: Light RTM utilizes lower-cost molds compared to traditional Resin Transfer Molding (RTM), making it an attractive option for low to medium-volume production runs.
- Enhanced Surface Finish: The closed-mold process produces parts with smooth surfaces on both sides, reducing the need for post-processing and improving aesthetic quality.
- Improved Dimensional Accuracy: The rigid mold setup ensures consistent part dimensions, which is crucial for applications requiring tight tolerances.
- Reduced Emissions: Operating within a closed mold significantly lowers styrene emissions, contributing to a safer and more environmentally friendly workplace.
- Versatility: Light RTM is suitable for producing large and complex parts, making it ideal for industries such as marine, automotive, aerospace, and construction.
The Light RTM Process in Detail
- Preparation of Fiber Reinforcements: Dry fibers are carefully arranged in the base mold to achieve the desired structural properties. Materials commonly used include fiberglass, carbon fiber, and aramid in various forms such as mats, woven fabrics, or stitched formats.
- Mold Assembly and Sealing: The counter mold is aligned over the base mold, and vacuum pressure is applied to seal the molds together. Vacuum rings around the tools assist in maintaining the seal during the process.
- Resin Injection: Catalyzed resin is introduced into the mold cavity under vacuum, ensuring complete saturation of the fiber reinforcements. Resins used can include polyester, vinyl ester, epoxy, or phenolic, depending on the application requirements.
- Curing: The resin is allowed to cure within the mold, solidifying the composite structure. Proper control of gel time is essential to prevent issues such as resin flow into the vacuum system.
- Demolding: Once cured, the counter mold is removed, and the finished part is extracted from the base mold. The part typically requires minimal finishing due to the high-quality surface achieved through the process.
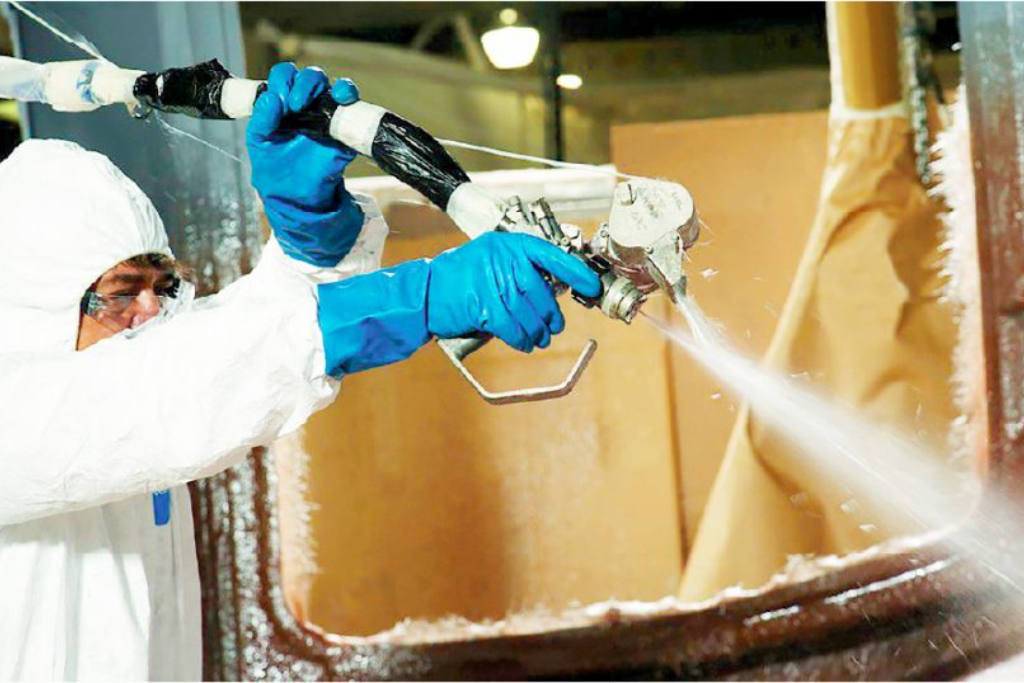
Applications of Light RTM
Light RTM is employed across various industries to manufacture components that benefit from its unique advantages:
- Marine Industry: Production of boat hulls, decks, and other structural components that require durability and a smooth finish.
- Automotive Sector: Manufacturing of lightweight body panels and structural parts that contribute to overall vehicle weight reduction.
- Aerospace: Fabrication of interior components and structural elements where weight savings and precision are critical.
- Construction: Creation of architectural elements, panels, and structural supports that benefit from corrosion resistance and design flexibility.
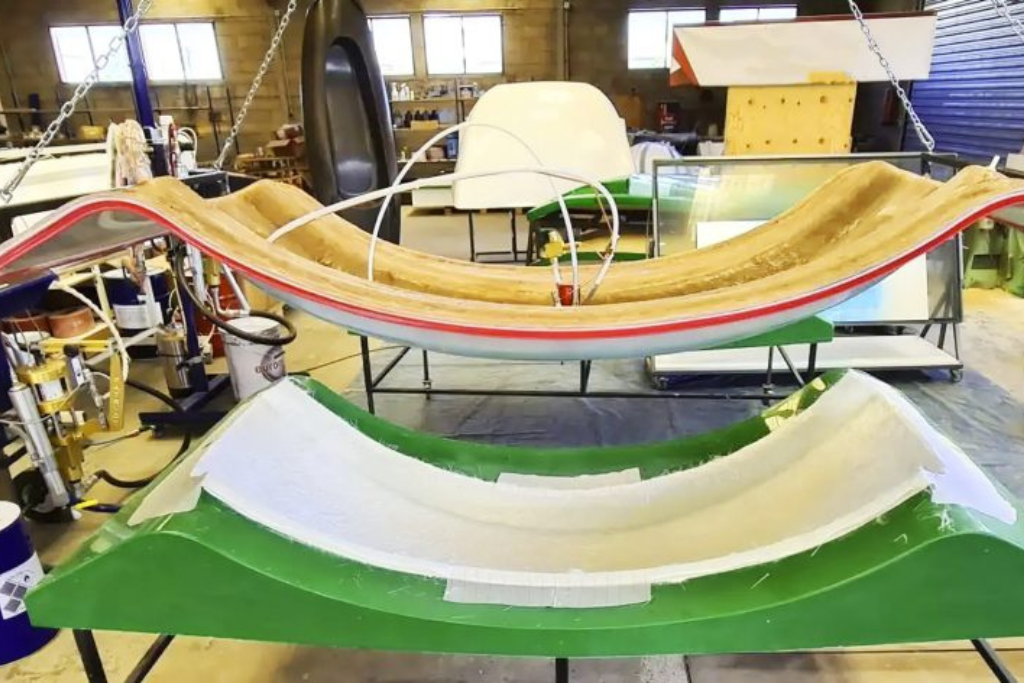
Transitioning to Light RTM
For manufacturers currently utilizing open molding techniques, transitioning to Light RTM can offer significant benefits, including improved product quality, reduced emissions, and enhanced workplace safety. The process is adaptable and can be implemented with relatively simple equipment, making it accessible for various production scales.
Vietnam is rapidly advancing in composite manufacturing, with companies like The Front leading the way in adopting cutting-edge technologies such as Light RTM. By utilizing this innovative process, The Front delivers high-quality, durable, and cost-effective composite products tailored to diverse industries, from marine and automotive to construction and energy. Their expertise in Light RTM not only ensures superior product performance but also aligns with global standards for sustainability and efficiency. Partnering with forward-thinking companies like The Front enables businesses to access world-class composite solutions while contributing to Vietnam’s growing presence in the global manufacturing landscape.