At THE FRONT, we don’t just manufacture – we engineer value. Light RTM (Light Resin Transfer Molding) is at the core of our advanced OEM composite solutions. This cutting-edge closed-mold technology delivers consistent quality, smooth surface finish, and scalable production – making it ideal for automotive, marine, and infrastructure applications.
1. Introduction to Light RTM Technology in OEM Composite Manufacturing
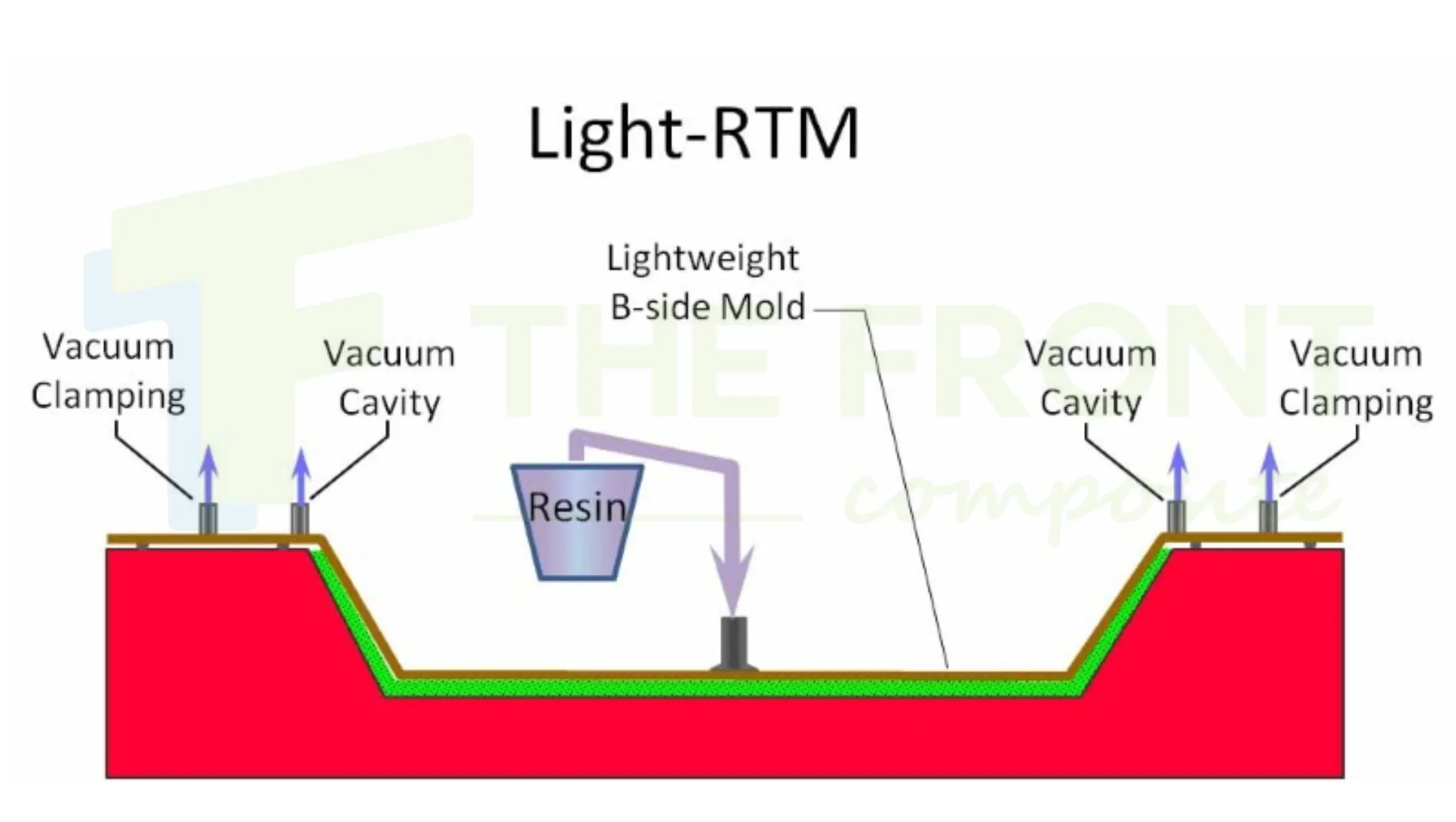
Light RTM (Light Resin Transfer Molding) is an advanced composite manufacturing method, widely used in the OEM (Original Equipment Manufacturer) composite product industry. Based on the principle of injecting resin into a closed mold under low pressure, this technology allows for the production of composite products with high strength, excellent surface quality, and efficient mass production capabilities.
Compared to other composite manufacturing methods such as Hand Lay-up, RTM (Resin Transfer Molding), and Pultrusion, Light RTM offers significant advantages. While Hand Lay-up requires manual labor to lay fibers and resin layer by layer, Light RTM offers a higher level of automation, reducing labor costs and production time. RTM, though similar, demands higher pressure, and Pultrusion is mainly used for simpler-shaped products. Light RTM stands out with its ability to create complex details and superior surface finishes that are difficult to achieve with other techniques.
The benefits of Light RTM in OEM composite production include cost optimization, improved product quality, and enhanced productivity. Notably, Light RTM minimizes material waste, increases manufacturing efficiency, and reduces environmental impact.
2. OEM Composite Manufacturing Process Using LRTM Technology
The OEM composite manufacturing process using LRTM technology consists of several fundamental steps, each playing a critical role in delivering high-quality products:
Step 1: Mold Design – Optimizing Shape and Strength
The mold determines the final shape and durability of the product. It must be designed with high precision and strength while optimizing resin flow and even distribution during injection.
Step 2: Preparation of Reinforcement Fibers and Resin Materials
Fiberglass or other reinforcing materials are carefully prepared to ensure product durability. The selected resin must be compatible with the reinforcement materials to ensure smooth processing.
Step 3: Mold Assembly and Vacuum System Setup
The mold is tightly assembled to prevent resin leakage during injection. A vacuum system is established to eliminate air, ensuring thorough resin penetration into the reinforcement layers.
Step 4: Low-Pressure Resin Injection for Even Impregnation
Resin is injected into the mold under low pressure, allowing it to saturate all gaps between the reinforcement fibers without creating air bubbles, resulting in a smooth, strong finished surface.
Step 5: Curing Process – Controlling Temperature and Time
Once the mold is fully injected, the curing process begins. Temperature and curing time must be carefully controlled to ensure the resin hardens properly, achieving superior mechanical and physical properties.
Step 6: Demolding, Surface Finishing, and Quality Inspection
Finally, the product is removed from the mold and undergoes surface finishing processes such as polishing and trimming, followed by quality inspection to meet technical standards.
3. Advantages of Light RTM Technology in OEM Composite Production
Light RTM technology brings a range of outstanding advantages compared to other composite manufacturing methods:
- High Surface Quality: Products have a smooth, glossy surface with no air pockets, reducing post-processing costs and enhancing aesthetic appeal.
- High Precision: Light RTM ensures manufacturing accuracy, minimizing deformation and consistently meeting technical standards.
- Material Savings: The precise and optimized resin injection significantly reduces resin and fiberglass usage.
- Environmental Friendliness: The LRTM process limits VOC (Volatile Organic Compounds) emissions, minimizing environmental impact compared to other methods.
4. Applications of OEM Composite Products Manufactured with Light RTM
Light RTM technology has proven versatile across a wide range of industries:
- Automotive Industry: Manufacturing components like bumpers, body panels, and hoods.
- Marine Industry: Producing parts like boat hulls and propeller blades to enhance durability and reduce weight.
- Energy Industry: Manufacturing wind turbine blades that require high strength and light weight.
- Industrial and Construction Sectors: Producing composite panels, chemical tanks, and equipment casings, enhancing product performance and durability.
5. Why LRTM is the Optimal Solution for OEM Composites
Light RTM stands out as the optimal solution for OEM composite production thanks to its numerous advantages:
- High-volume Production with Consistent Quality: Light RTM ensures consistent quality across batches, reducing variation and maintaining high precision.
- Reduced Labor Costs and Increased Productivity: Its high automation level reduces reliance on manual labor, boosting productivity and lowering costs.
- Optimized Weight and Strength: Products can be optimized in design, achieving lightweight characteristics without compromising strength.
6. Conclusion – LRTM Shapes the Future of OEM Composite Manufacturing
Light RTM technology is increasingly becoming the leading trend in composite manufacturing, offering remarkable benefits in quality, efficiency, and cost. With the ability to optimize production processes and improve product quality, Light RTM will continue to play a crucial role in enhancing the competitiveness of composite manufacturers.
THE FRONT is committed to applying Light RTM technology in the production of OEM composite products in Vietnam, delivering high-quality, durable, and environmentally friendly solutions to its customers.
You can read more in there.
THE FRONT JSC
Address: Block H19, St. N1, Nam Thuan Industrial Park, Duc Hoa Dong Ward, Duc Hoa District, Long An Province
Hotline: +(84)96-888-7363
Email: [email protected]