Modern construction and engineering industries are always looking for materials that combine strength, flexibility, corrosion resistance, and cost-efficiency. One such material rising in popularity across a wide range of structural applications – including those in Vietnam – is the pultrusion composite.
By using pultrusion composites, builders and engineers can deliver structures that last longer, perform better, and require far less maintenance compared to traditional materials like steel, aluminum, or wood – a major advantage for infrastructure development in Vietnam.
In this article, we’ll dive into what pultrusion composites are, why they’re becoming the go-to solution for modern structures, and explore the key benefits that make them a smarter choice for your next project.
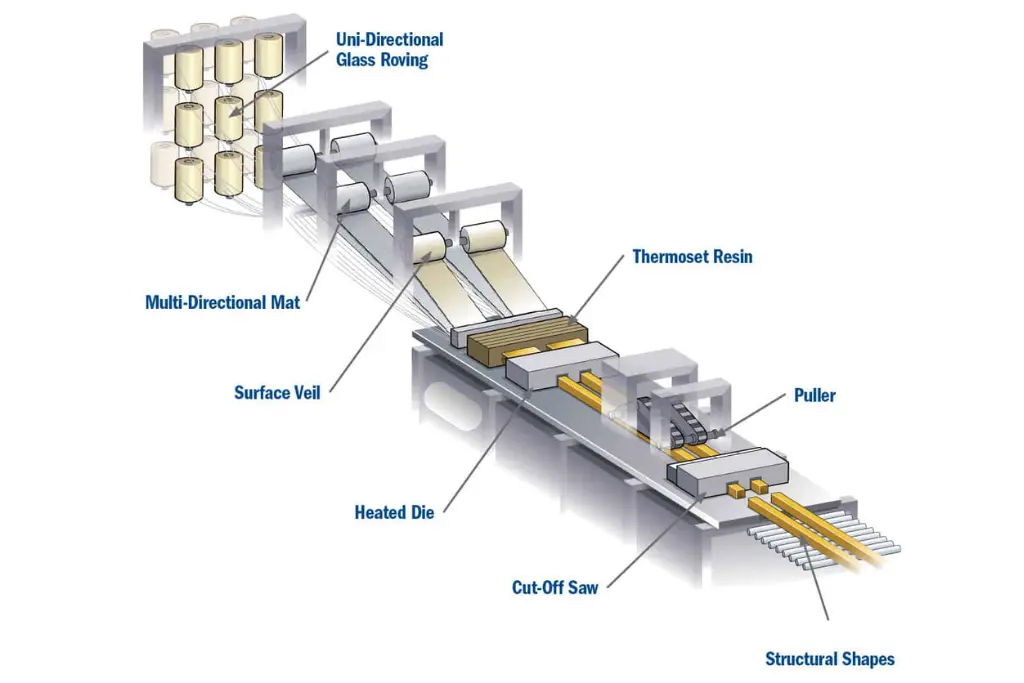
What is a Pultrusion Composite?
A pultrusion composite is a fiber-reinforced polymer material produced through a continuous manufacturing process known as pultrusion. During this process, strong fibers (typically fiberglass) are pulled through a resin bath and then a heated die, where they are shaped and cured into long, strong, and consistent profiles.
The result is a lightweight, extremely durable material that can be manufactured into beams, rods, tubes, and custom profiles – all offering remarkable mechanical strength and resistance to environmental damage.
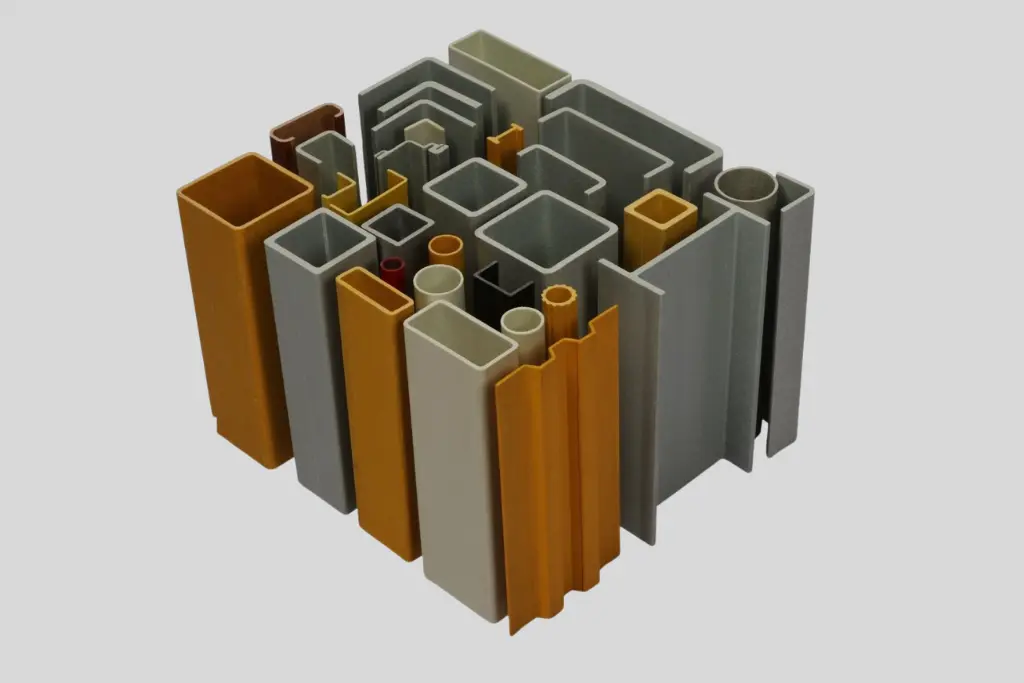
Key Benefits of Pultrusion Composites in Structural Applications
1. Superior Strength-to-Weight Ratio
One of the biggest advantages of pultrusion composites is their outstanding strength-to-weight ratio. They are often 70% lighter than steel while maintaining similar, or even superior, mechanical properties in certain applications.
This makes pultrusion composites ideal for:
- Structural frameworks
- Platforms and walkways
- Bridges and decks
- Reinforced beams and girders
Using lighter materials reduces the load on foundations, simplifies transportation, and speeds up installation – all without compromising structural integrity.
2. Corrosion Resistance
In environments exposed to water, chemicals, salt, or industrial pollutants, traditional materials like steel quickly corrode, leading to high maintenance costs and potential structural failures.
Pultrusion composites are inherently corrosion-resistant. They do not rust, rot, or degrade when exposed to harsh conditions, making them perfect for:
- Coastal structures
- Wastewater treatment plants
- Chemical facilities
- Offshore oil platforms
Switching to pultrusion composites extends the service life of structures while drastically reducing the need for coatings, paints, or costly repairs.
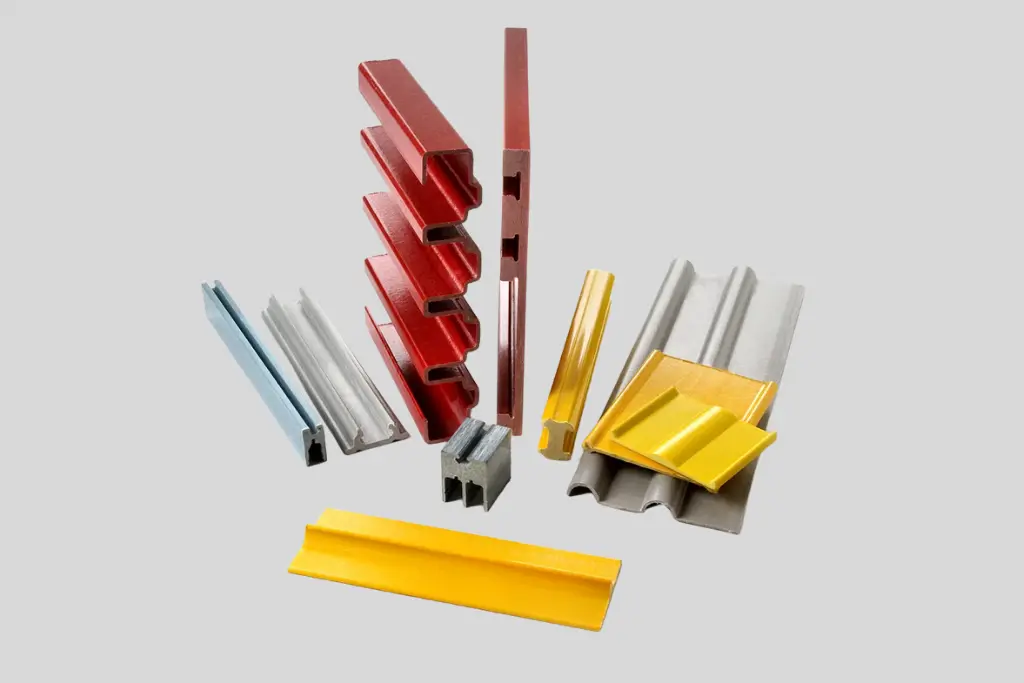
3. Low Maintenance Costs
Structures built with pultrusion composites require minimal maintenance over their lifetime. Unlike metal, they don’t need regular repainting or rust treatment. Unlike wood, they won’t require resealing or replacement due to rot or insect damage.
This leads to:
- Lower lifecycle costs
- Less downtime for repairs
- Greater predictability in maintenance budgets
For municipalities, industries, and commercial property owners, lower maintenance means significant long-term savings.
4. High Dimensional Stability
Pultrusion composites offer excellent dimensional stability. They expand and contract far less than metals or plastics when exposed to temperature fluctuations.
This stability is crucial for structures that experience wide thermal swings, such as:
- Bridges
- Outdoor platforms
- Aerospace structures
- Transportation infrastructure
With pultrusion composites, you avoid structural shifts, misalignments, and stress fractures caused by thermal expansion and contraction.
5. Electrical and Thermal Insulation
Pultrusion composites are naturally non-conductive. This makes them especially valuable in applications where electrical insulation is required, including:
- Power plants
- Electrical substations
- Telecommunications towers
- Train and metro systems
Moreover, they offer low thermal conductivity, contributing to better energy efficiency and safer handling in industrial environments.
6. Design Flexibility
Another huge benefit of using pultrusion composites in structural applications is the wide range of design options. They can be manufactured in almost any profile, including:
- I-beams
- Channels
- Angles
- Flat sheets
- Round tubes
Custom shapes and sizes are also easy to produce, allowing engineers and architects greater flexibility in creating innovative designs without being restricted by material limitations.
7. Environmental Sustainability
With increasing attention on sustainable construction, pultrusion composites offer environmental advantages as well:
- Long service life reduces resource consumption
- Lightweight profiles cut down on fuel and emissions during transport
- Many composites use resins with recycled content or bio-based ingredients
Additionally, because structures made with pultrusion composites require less maintenance and fewer replacements, the environmental impact over the structure’s life cycle is significantly lower than that of traditional materials.
Common Structural Applications of Pultrusion Composites
Because of their versatility and performance, pultrusion composites are used in a wide variety of industries and structures, including:
- Building and construction: Structural frames, curtain walls, window and door profiles
- Infrastructure: Bridge decks, guardrails, pedestrian walkways
- Industrial plants: Support structures, safety handrails, chemical tanks
- Marine environments: Docks, piers, underwater structures
- Transportation: Components for buses, trains, and aircraft
- Energy sector: Cable trays, support racks, wind turbine blades
No matter the industry, pultrusion composites are proving to be a smarter, more durable alternative.
Why Pultrusion Composites Are Replacing Traditional Materials
When you look at the full picture – strength, weight, durability, cost savings, and sustainability – it’s easy to see why pultrusion composites are gaining popularity. They provide solutions to the most pressing challenges in modern construction and infrastructure projects, from corrosion issues to maintenance cost control.
Projects that historically relied on steel, aluminum, or timber are increasingly turning to pultrusion composites to enhance performance while reducing overall lifecycle costs.
Choosing the right materials is critical to the success of any structural project. When you prioritize durability, energy efficiency, design flexibility, and low maintenance – especially for projects in Vietnam – pultrusion composites clearly stand out.
For builders, engineers, and facility managers seeking a future-proof solution, integrating pultrusion composites into structural applications isn’t just smart – it’s essential, particularly in Vietnam’s demanding industrial and infrastructure sectors.
If you’re ready to explore how pultrusion composites can improve your next project, The Front offers top-quality pultrusion composite solutions built for today’s toughest environments in Vietnam and beyond.