In recent years, FRP panels (Fiber Reinforced Plastic panels) have become increasingly popular in construction, industrial, and commercial applications. Known for their durability, lightweight nature, and corrosion resistance, FRP panels are a versatile choice for a wide range of projects. However, with so many options available, it can be challenging to select the best FRP panel for your specific needs. In this guide, we’ll break down key factors to consider when choosing FRP panels to ensure you make the best decision for your project.
What Are FRP Panels?
Before diving into how to choose the right FRP panels, let’s quickly cover what they are. FRP panels are composite materials made from a polymer matrix (often polyester or vinyl ester resin) reinforced with fibers (usually fiberglass). The result is a panel that is strong, lightweight, and resistant to environmental and chemical damage. These properties make FRP panels ideal for applications in sectors like construction, transportation, water treatment, food processing, and more.
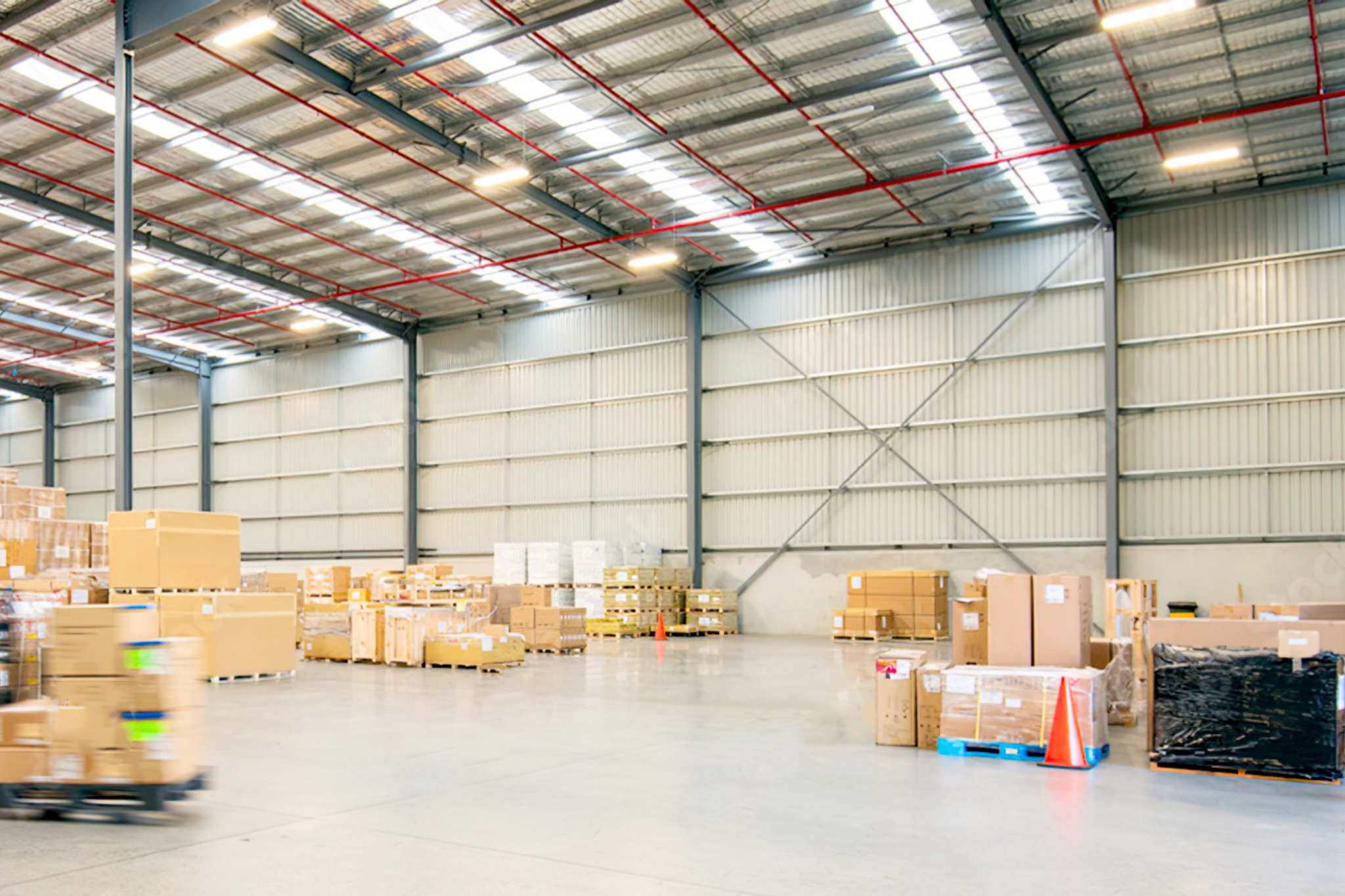
Why FRP Panels Are a Popular Choice
FRP panels offer several benefits compared to traditional materials such as wood, metal, and concrete:
- Corrosion Resistance: FRP panels don’t rust, rot, or degrade in harsh conditions, making them ideal for outdoor and industrial applications.
- Lightweight Yet Strong: They are lighter than metals and concrete, reducing transportation costs and easing installation, while still providing excellent strength.
- Low Maintenance: Due to their durability, FRP panels require minimal maintenance, which reduces long-term costs.
- Versatile Applications: From wall panels and ceiling coverings to flooring, tanks, and roofing, FRP panels can be tailored to meet specific project requirements.
With these benefits in mind, let’s look at the critical factors to consider when choosing the right FRP panels.
1. Identify Your Project’s Specific Requirements
The first step in choosing the right FRP panels is understanding the specific needs of your project. Start by asking the following questions:
- What environment will the panels be exposed to? (e.g., outdoor, indoor, chemical exposure, high humidity)
- What level of strength and durability is required?
- Are aesthetics important, or is functionality the primary concern?
Understanding these aspects will help you determine the type and specifications of FRP panels that will best meet your project’s demands.
2. Consider the Resin Type
Choosing the right resin type is crucial to ensure that your FRP panels meet the specific demands of your project. Each resin type offers distinct advantages, depending on the environment and application. Here’s an overview of the resin types available, highlighting their strengths and best uses:
- Polyester Resin: Known for being a cost-effective option, polyester resin is widely used for general-purpose FRP panels. It provides moderate chemical resistance and is ideal for applications that don’t involve constant exposure to harsh chemicals or corrosive environments. This resin is suitable for indoor applications, decorative panels, and areas with limited chemical exposure. THE FRONT’s FRP panels made with polyester resin offer the perfect balance between performance and affordability, making them a popular choice for projects where cost efficiency and dependable quality are key. THE FRONT’s expertise in resin formulation ensures that these panels maintain their integrity and appearance over time, even in challenging indoor environments.
- Vinyl Ester Resin: If your project requires high chemical resistance, vinyl ester resin is the optimal choice. This resin type is designed to withstand exposure to a wide range of corrosive substances, including acids, alkalis, and other harsh chemicals. It also offers excellent impact resistance and durability. Vinyl ester resin is ideal for industrial settings where panels may come into contact with corrosive materials, such as chemical plants, wastewater facilities, and environments with high humidity.
Selecting the correct resin type based on your project’s exposure to chemicals, temperature, and environmental conditions will enhance the performance and lifespan of your FRP panels.
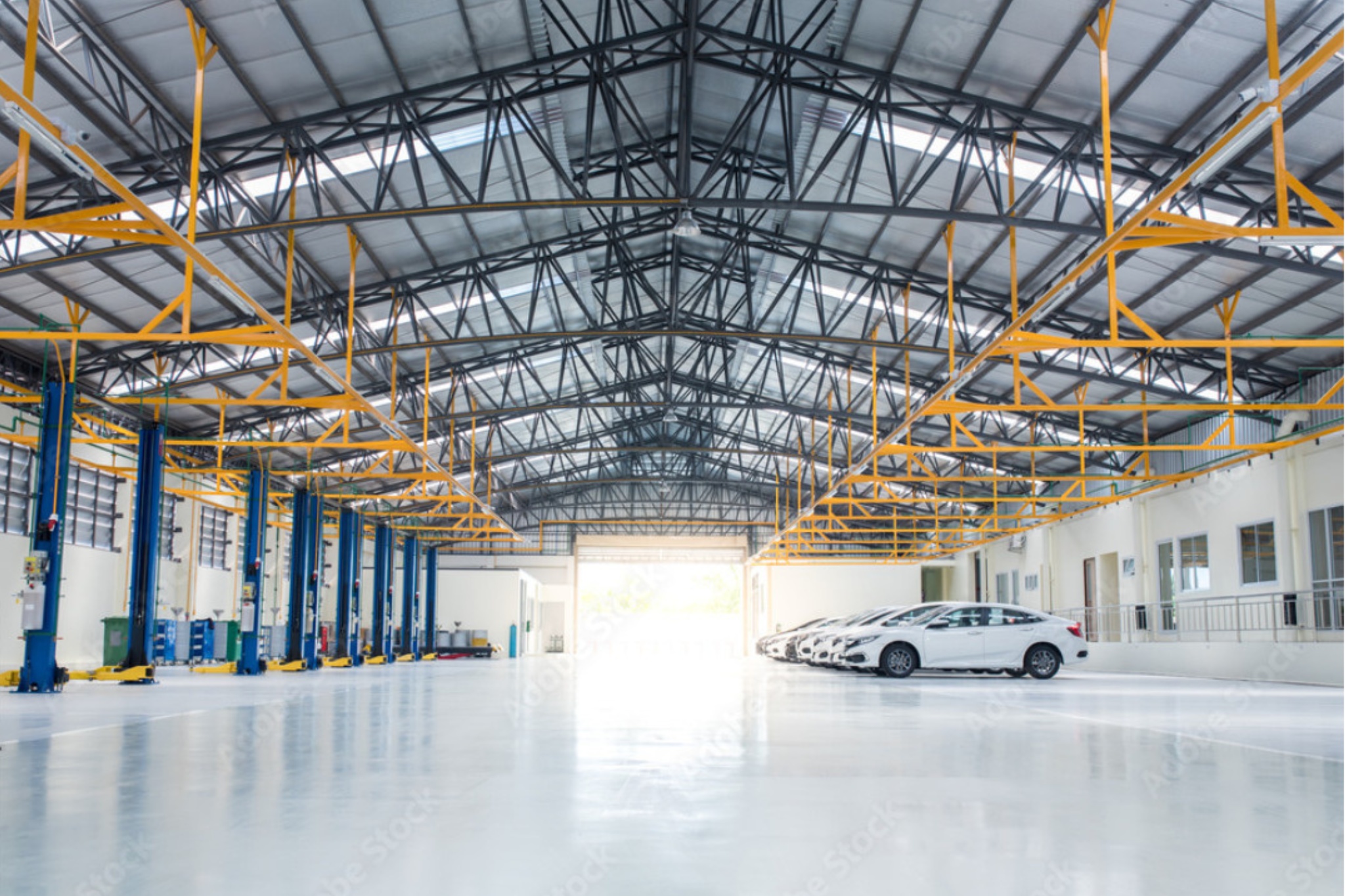
3. Determine the Panel Thickness
FRP panels come in various thicknesses, which affect their strength, durability, and cost. Thicker panels generally offer more durability and load-bearing capacity, but they are also heavier and more expensive. Here’s how to determine the right thickness for your project:
- Light-Duty Applications: For decorative or wall-covering applications where there isn’t significant weight or impact, a thinner FRP panel (around 1-2 mm) may suffice.
- Medium-Duty Applications: If your project involves moderate loads or light foot traffic, consider medium-thickness FRP panels (around 3-4 mm).
- Heavy-Duty Applications: For flooring, roofing, or industrial environments that require impact resistance, thicker FRP panels (5 mm and above) are recommended.
Assess the demands of your project to choose the appropriate thickness that balances performance with cost.
4. Evaluate Surface Finishes and Textures
FRP panels are available with various surface finishes and textures, each suited to different applications. The right finish can enhance the functionality and appearance of the panels:
- Smooth Finish: Smooth surfaces are easy to clean and are often used in food processing areas, kitchens, and healthcare facilities. They provide a hygienic surface that resists mold, mildew, and bacteria growth.
- Textured or Embossed Finish: A textured or embossed surface can provide anti-slip properties, making it suitable for flooring, walkways, and areas exposed to moisture.
- UV-Protective Coating: For outdoor applications, consider FRP panels with a UV-resistant coating to prevent yellowing, fading, and degradation from sun exposure.
- Fire-Resistant Coating: Some FRP panels are available with fire-resistant coatings, which are essential for applications that need compliance with fire safety standards.
Choosing the right surface finish and texture will enhance the panel’s performance and appearance according to your project needs.
5. Choose the Right Color and Transparency Level
FRP panels come in various colors and transparency levels. Consider whether you need translucent panels to allow light through, or opaque panels for privacy or aesthetic reasons.
- Translucent Panels: These panels allow natural light to filter through, making them a popular choice for roofing and skylights in industrial buildings, greenhouses, and warehouses. Translucent panels reduce the need for artificial lighting, improving energy efficiency.
- Opaque Panels: For applications where light transmission is not needed, opaque panels in various colors can enhance the aesthetics of a building or structure. They are often used as wall cladding, partitions, or decorative facades.
Choose the color and transparency based on the functional and aesthetic goals of your project.
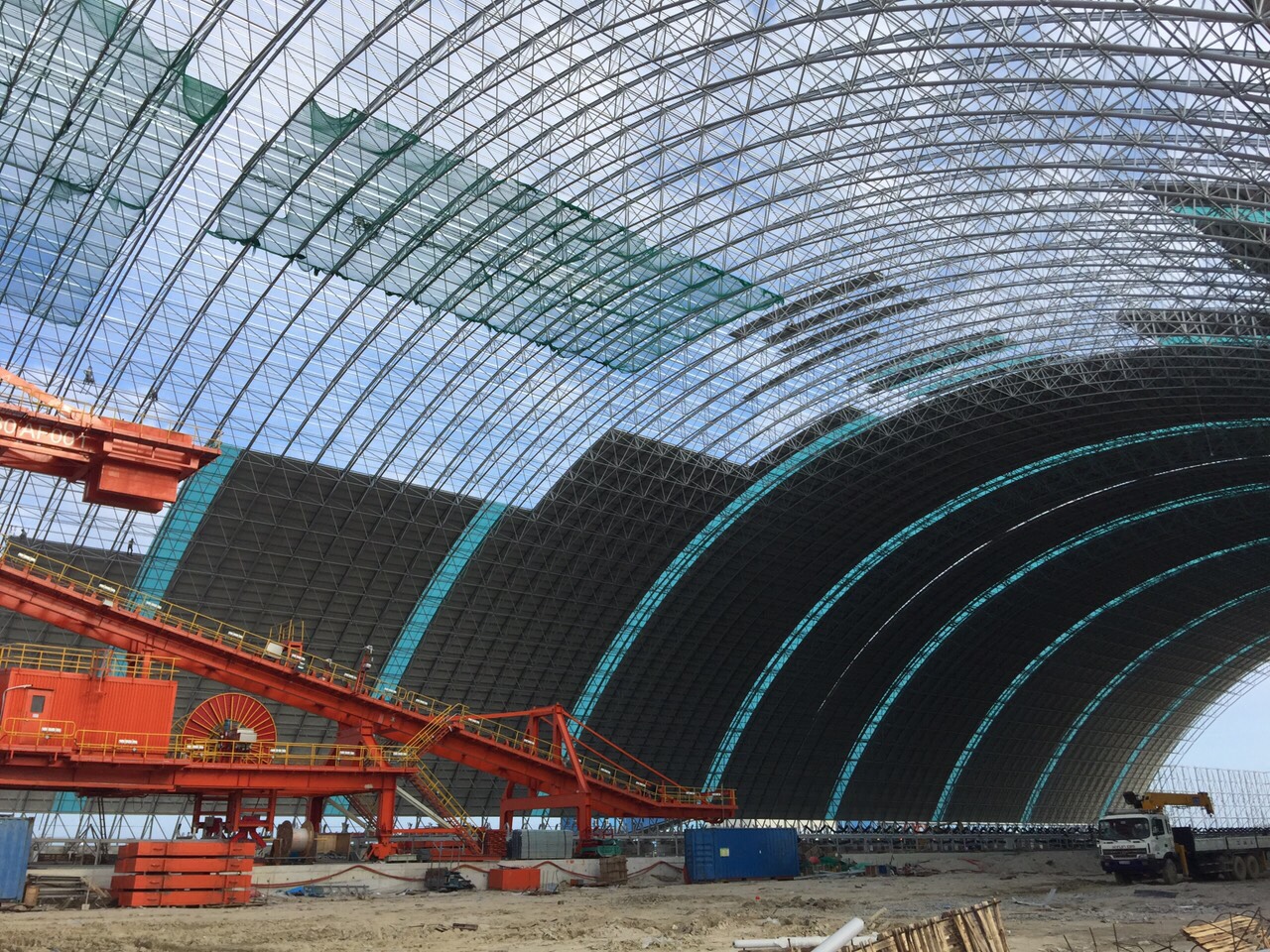
6. Assess Installation Requirements
Some FRP panels are easier to install than others, depending on their weight, flexibility, and fastening system. Consider the installation process, especially if you have specific requirements such as:
- Ease of Cutting and Shaping: Certain FRP panels can be easily cut and customized on-site, while others may require specialized tools.
- Fastening Compatibility: Ensure the panels are compatible with the roofing or wall systems used in your project.
- Thermal Expansion: FRP panels expand and contract with temperature changes, so make sure to allow for expansion gaps during installation to avoid warping or buckling.
Work with your contractor or installation team to select FRP panels that fit your installation needs and budget.
7. Budget and Long-Term Costs
Finally, consider the budget for your project and the long-term costs associated with maintenance and replacement. While FRP panels may have a higher upfront cost than some traditional materials, their durability and low maintenance often make them a cost-effective choice over time.
- Initial Cost: Choose panels that meet your project’s requirements without exceeding the budget. Compare prices based on resin type, thickness, and surface finish.
Long-Term Savings: Remember that FRP panels are low-maintenance and highly durable, which can save you money on repairs and replacements in the long run.
Making the Right Choice for Your FRP Panels
Selecting the right FRP panels for your project involves assessing factors such as environment, resin type, thickness, surface finish, and budget. By carefully considering these elements, you can choose panels that meet your specific requirements, ensure durability, and maximize cost-effectiveness. Whether you’re building a warehouse, greenhouse, or industrial facility, the right FRP panels can significantly enhance your project’s performance and longevity.
If you’re looking for high-quality, customized FRP panels, THE FRONT is a trusted manufacturer with decades of experience in delivering top-tier FRP solutions. With a commitment to quality and innovation, THE FRONT offers a wide range of FRP panels tailored to meet the unique demands of various projects. Their expert team is ready to guide you through the selection process, ensuring you choose the ideal product for your needs. Make a smart, lasting choice with THE FRONT’s FRP panels and experience the long-lasting benefits they bring to your construction projects.