Bridges are not just structures; they are lifelines connecting communities, industries, and economies. In industrial settings where environmental conditions are harsh and maintenance costs are high, traditional construction materials often fall short. Enter pultruded FRP (Fiber Reinforced Polymer) profiles – a modern engineering solution offering unmatched strength, corrosion resistance, and longevity. This article explores how pultruded FRP profiles are transforming industrial bridge design across the globe.
What Are Pultruded FRP Profiles?
Pultrusion is a continuous manufacturing process that produces fiber-reinforced polymer profiles with consistent cross-sectional shapes. In this process, continuous strands of fiberglass (or other reinforcing fibers) are pulled through a resin bath and then through a heated die to form rigid, high-performance structural shapes.
Common profiles include:
- I-beams
- Channels
- Angles
- Box sections
- Flat plates
These profiles exhibit high tensile strength, dimensional stability, and superior durability in aggressive environments.

Key Strength Benefits in Bridge Design
- High Strength-to-Weight Ratio: Pultruded FRP profiles offer exceptional strength without the weight burden of steel or concrete. This enables easier transportation, quicker installation, and reduced need for heavy lifting equipment. For temporary or modular bridges, this characteristic is especially valuable.
- Corrosion Resistance: Unlike steel, FRP profiles do not rust or corrode when exposed to chemicals, saltwater, or moisture. This makes them ideal for bridges in coastal, marine, and chemical plant environments where corrosion can compromise structural integrity and safety.
- Design Flexibility: Engineers can customize pultruded profiles to fit exact load and geometric requirements. This adaptability allows FRP structures to integrate seamlessly into both retrofits and new builds, often with better performance than conventional materials.
- Fatigue Resistance: FRP materials exhibit excellent fatigue resistance, meaning they can endure cyclic loading without degrading over time. This is critical in bridge applications where vehicles and equipment create dynamic, repetitive stresses.
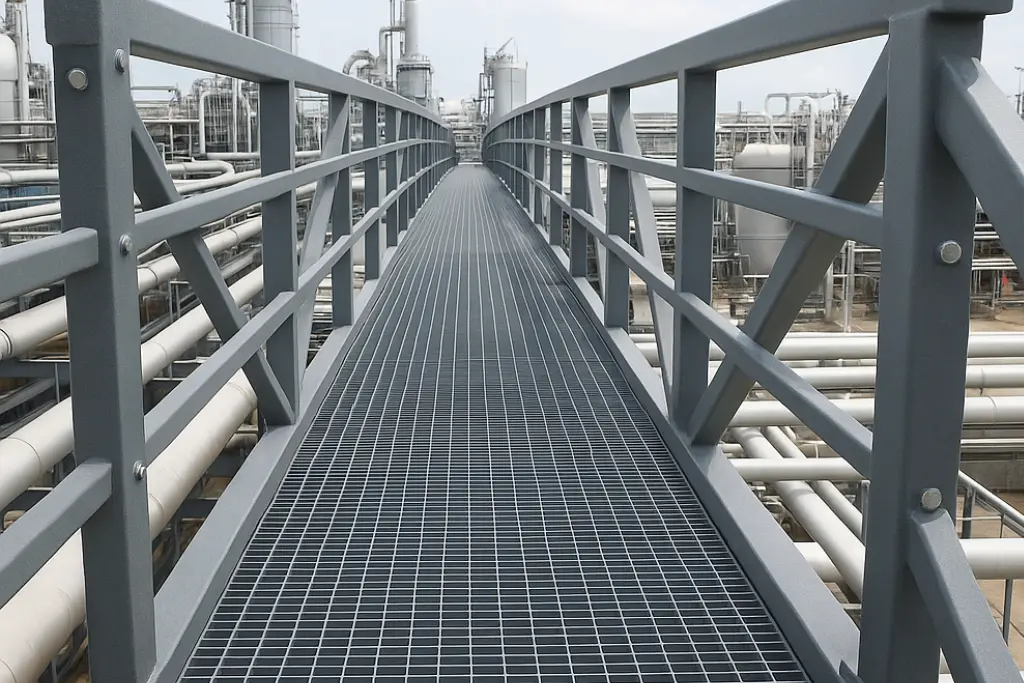
Practical Applications in Industrial Bridges
- Pedestrian and Access Bridges: Pultruded FRP walkways and access bridges are used in factories, offshore platforms, and refineries. Lightweight and low-maintenance, they offer safe passage over hazardous zones.
- Pipe Support Bridges: In facilities with extensive piping systems (e.g., chemical plants), FRP bridges provide strong, non-conductive support for elevated pipe networks.
- Vehicular Bridges: While less common, FRP materials are increasingly used in vehicular bridge decks, especially where weight limits and corrosion concerns dictate the need for alternative materials.
Case Example: Chemical Plant Access Bridge A chemical plant in Southeast Asia needed to replace a corroded steel access bridge. The client opted for a pultruded FRP bridge due to its resistance to acid fumes and minimal maintenance requirements. The installation was completed in half the time of a steel structure, and the bridge has since required no repainting or repair despite constant chemical exposure.
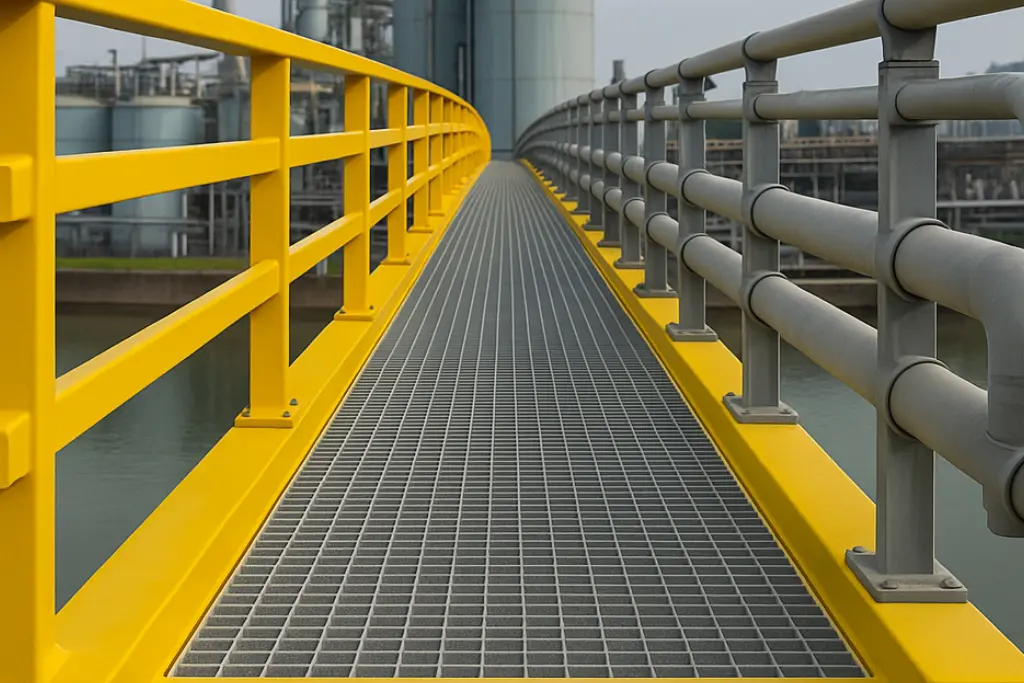
Environmental and Economic Benefits
- Lower Lifecycle Costs: While the initial cost of FRP profiles can be higher than steel, the total cost of ownership is significantly lower due to reduced maintenance and longer service life.
- Sustainable Construction: FRP profiles are produced with less energy than traditional metals and are recyclable in many cases.
- Minimal Downtime: Lightweight materials allow faster installations, reducing plant downtime or traffic disruptions during bridge construction.
Pultruded FRP profiles are more than an alternative to traditional materials—they represent a step forward in bridge engineering. Their strength, stability, and resistance to harsh conditions make them ideal for industrial bridge designs worldwide. As demand grows for durable, low-maintenance infrastructure, pultruded FRP profiles are proving to be a smart investment in both performance and longevity.
Explore Our Solutions At The Front Company, we manufacture and export high-quality pultruded FRP profiles designed to meet the toughest industrial standards. Contact us today to learn how our FRP solutions can reinforce your next bridge project.