Have you ever had trouble with metal floors that rust, become slippery, or are difficult to maintain? If so, composite grating might be the solution you’re looking for: it’s lighter, more durable, and corrosion-resistant—ideal for projects that demand long-term performance and low maintenance costs.
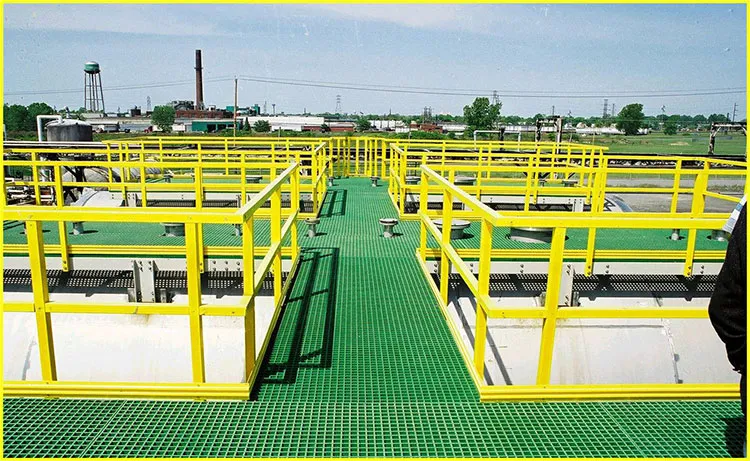
1. Introduction to Composite Grating
Composite grating—also known as fiberglass reinforced plastic (FRP) grating—is increasingly becoming the preferred alternative to traditional metal grating across various industrial sectors. Made primarily from engineered resins (typically polyester) combined with reinforced fiberglass, composite grating offers outstanding advantages in both durability and corrosion resistance.
Unlike steel grating, which is prone to rust, composite grating is virtually immune to harsh environments, especially acids, salts, and industrial solvents. As a result, it significantly reduces maintenance costs and extends the lifespan of installations.
Today, composite grating is widely used in industries such as chemicals, oil & gas, marine, water treatment, and construction, thanks to its flexibility and long-term efficiency.
2. Composite Grating Manufacturing Technology
One of the most common methods for producing this is the molded grating technique.
The production process begins by pouring a mixture of liquid resin and fiberglass into a mold. The system then compresses and cures the mixture to form a strong lattice structure.
A key feature of this method is the uniform structure in both directions, giving the grating excellent load-bearing capacity and stability under various installation conditions.
3. Composite Grating Production Process
This is known not only for its durable structure but also for being manufactured through a strict process to ensure superior quality:
- Step 1: Material Preparation
High-quality polyester resin and fiberglass are carefully selected to ensure the product’s durability and load-bearing capabilities. - Step 2: Forming the Grating Structure
Molded or pultruded methods are applied to create the grid structure, tailored to the technical requirements of each project, ensuring flexibility in design and high precision. - Step 3: Resin Curing
The resin is cured in the mold under controlled temperature and time conditions, providing optimal strength, rigidity, and resistance to external forces. - Step 4: Cutting to Required Size
After curing, the composite grating is precisely cut to the required dimensions and shapes to suit specific applications. - Step 5: Surface Finishing and Quality Inspection
Finally, the surface is treated for smoothness and undergoes strict quality inspections to ensure the composite grating meets international standards before being delivered.
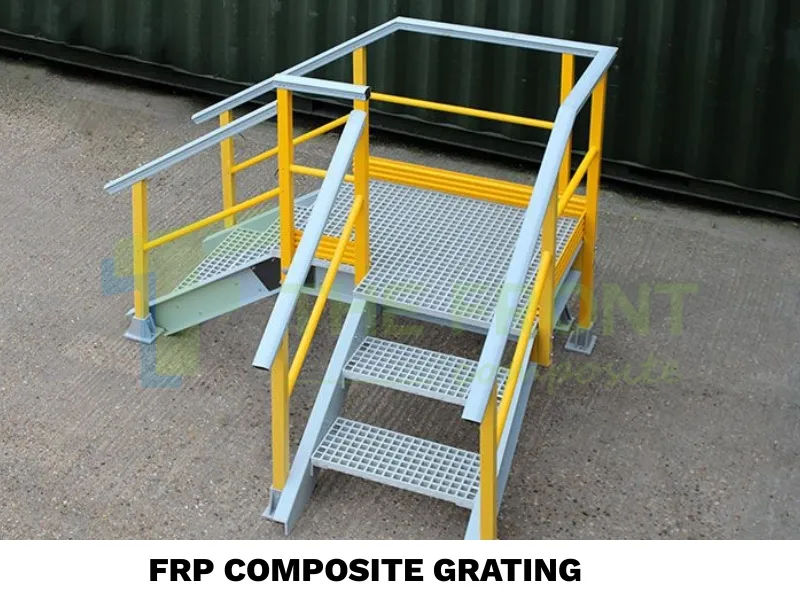
4. Advantages of Composite Grating
Composite grating is not just an ordinary product—it is the optimal solution for harsh environments, offering outstanding benefits:
- Superior Corrosion Resistance
This is completely rust-proof and resistant to chemicals, acids, and seawater, maintaining long-term effectiveness in highly corrosive environments. - Lightweight
Its light weight makes it easy to transport and install, reducing labor costs and minimizing the load on structures. - Excellent Electrical and Thermal Insulation
This provides excellent electrical and thermal insulation, ensuring absolute safety in workplaces involving electricity and heat—especially ideal for industrial and power facilities. - Simple Maintenance
Unlike steel grating, composite grating requires no regular painting or maintenance, greatly reducing upkeep costs and enhancing product longevity.
5. Applications of Grating
Thanks to its design flexibility and outstanding features, this is the ideal choice for a wide range of industries:
- Chemical Industry
Used for work platforms and manhole covers, offering excellent corrosion resistance when exposed to chemicals and harsh environments. - Oil & Gas Industry
Applied on offshore platforms and storage tank areas, meeting stringent standards for durability, load-bearing, and corrosion resistance. - Marine Industry
Popular for ship decks and port walkways due to its seawater resistance and superior durability in marine conditions. - Water Treatment & Environmental Sector
Installed in wastewater treatment plant walkways, ensuring durability and abrasion resistance in high-humidity, chemical-laden environments. - Construction Sector
Used in industrial flooring, railings, and non-slip stairs, enhancing safety and reducing maintenance costs in construction projects.
6. Composite Grating vs. Metal Grating Comparison
Composite grating is becoming increasingly favored in modern construction projects thanks to its significant advantages over traditional metal grating:
Criteria | Composite Grating | Metal Grating |
Corrosion Resistance | Excellent—Unaffected by chemicals and seawater | Prone to rust—Requires regular coating and protection |
Weight | Lightweight—Easy to transport and install | Heavy—Higher transportation and labor costs |
Electrical and Thermal Insulation | Yes—Safe for electrical and thermal environments | No—Conducts electricity, posing risks |
Load-Bearing Capacity | High—Meets various technical requirements | Very High—Suitable for extremely heavy loads |
Maintenance Costs | Low—Minimal maintenance required | High—Needs frequent inspection and anti-rust treatments |
7. Conclusion – Grating: The Future Solution
As industrial trends move toward more sustainable, cost-effective, and eco-friendly materials, composite grating has emerged as a superior solution, gradually replacing traditional metal grating.
With exceptional lifespan, near-zero maintenance costs, corrosion resistance, electrical and thermal insulation properties, composite grating not only addresses today’s demands but also paves the way for a safer, more economical future.
At THE FRONT, we proudly lead the market in providing international-grade composite grating systems that meet the most demanding technical standards. Our team is ready to support your next project with tailored solutions designed for durability, safety, and long-term value..
Contact us today for tailored solutions for your projects—more durable, safer, and more cost-effective starting now.