Discover the power of Spray-Up composite technology – a fast, flexible, and efficient method for producing high-quality FRP products. Ideal for complex shapes in marine, construction, and OEM manufacturing.
1. Introduction to Spray-Up Technology
What is Spray-Up?
Spray-Up, also known as fiber spraying technology, is one of the most popular and versatile composite manufacturing methods today. This technique uses a specialized spray gun to simultaneously spray a resin matrix (typically Polyester or Vinylester) and chop fiberglass strands directly onto the mold surface. The result is a continuous composite layer with high strength, excellent mold adhesion, and suitability for complex designs.
Spray-Up is particularly suitable for products with curved, asymmetrical shapes or those requiring mass production, such as tanks, boats, vehicle shells, sanitary equipment, or large industrial parts.
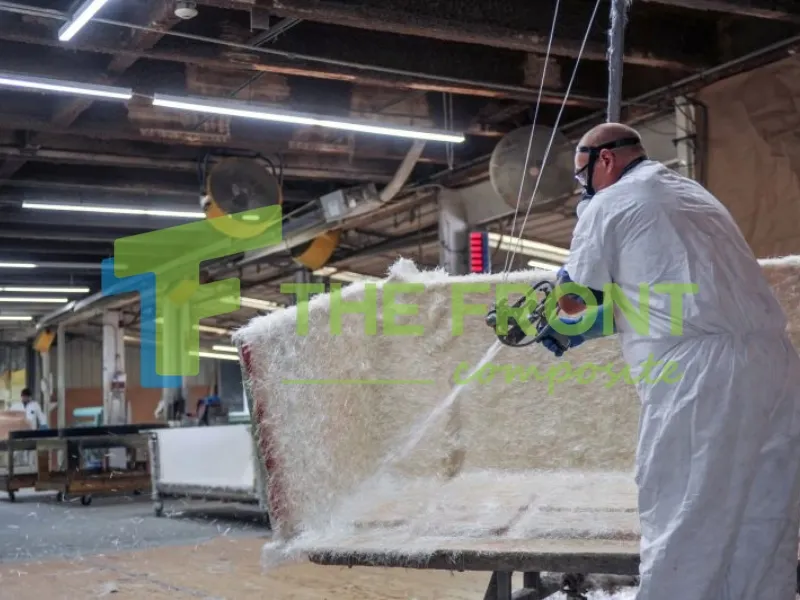
Development History of Spray-Up Technology
Spray-Up technology emerged in the mid-20th century amid growing demand for composite materials in industries such as marine, automotive, and construction. Initially based on simple manual systems, Spray-Up has since seen major advancements—from integrating automatic fiber chopping heads to incorporating intelligent control systems.
Today, Spray-Up not only speeds up production but also improves product quality, reduces material waste, and optimizes costs—becoming a leading choice for many composite manufacturers worldwide.
2. Operating Principle of Spray-Up Technology
Spray-Up works based on the principle of simultaneously spraying resin and reinforcing fibers onto the mold, creating a composite layer with a uniform structure and flexible shapes.
Step 1: Spraying resin and fiberglass onto the mold
Using a specialized spray gun, a mixture of resin (Polyester, Vinylester, or Epoxy) and chopped fiberglass is simultaneously sprayed onto the mold surface.
Step 2: Forming a bonded composite layer
During spraying, fibers and resin are mixed thoroughly, forming a continuous composite layer that adheres firmly to the mold, offering both lightweight properties and high mechanical strength.
Step 3: Rolling and compressing
After spraying, the material layer is gently rolled using a roller to eliminate air bubbles, ensuring consistent thickness and a smooth surface that meets technical requirements.
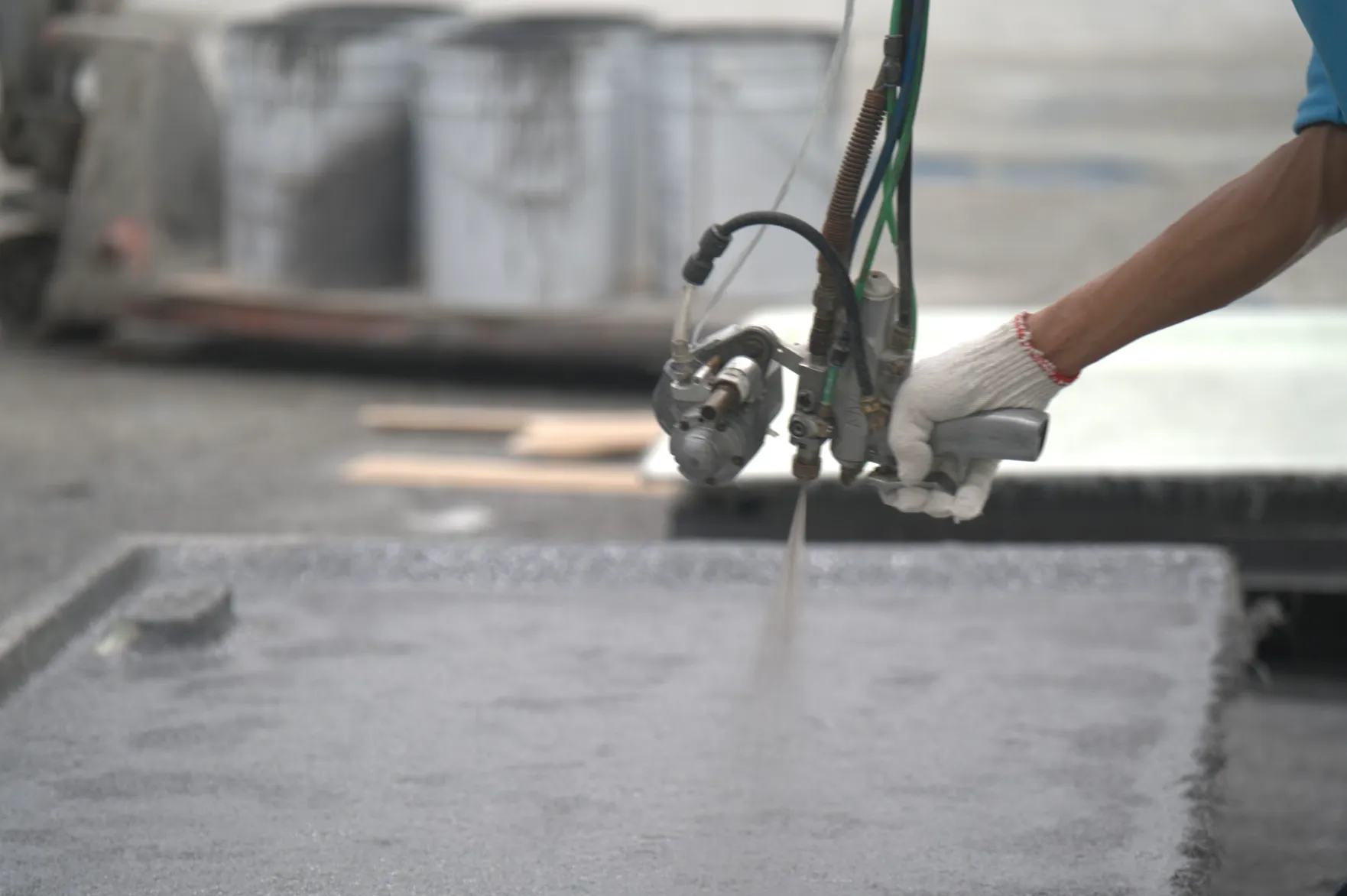
Comparison: Spray-Up vs. Other Composite Technologies
Công nghệ | Key Features |
Spray-Up | High automation, fast application speed, suitable for complex shapes |
Hand Lay-Up | Manual, easy to handle, flexible but labor-intensive and skill-dependent |
RTM (Resin Transfer Molding) | High precision, excellent surface finish, ideal for mass production of double-sided products |
Pultrusion | Produces continuous-shaped, high-strength products, ideal for large-scale manufacturing |
3. Composite Production Process Using Spray-Up Technology
The Spray-Up process involves multiple integrated steps to create complex-shaped, high-quality, durable composite products. Basic steps include:
Step 1: Mold preparation
Clean the mold thoroughly and apply a specialized release agent to prevent sticking, ensuring easy demolding after curing.
Step 2: Spraying resin and fiberglass
Use Spray-Up equipment to simultaneously spray the resin matrix (Polyester, Vinylester, Epoxy…) and chopped fiberglass onto the mold surface according to the desired thickness and shape.
Step 3: Rolling and compressing the material layer
Use a specialized roller to compress and smooth the composite layer, remove air bubbles, and ensure uniform thickness and even distribution.
Step 4: Curing
Depending on the type of resin used, curing can occur at room temperature or be accelerated with heating to shorten curing time and improve bond quality.
Step 5: Demolding and finishing
Once fully cured, the product is demolded. It then undergoes finishing processes such as trimming, drilling, and sanding, followed by quality inspection before packaging or installation.
4. Advantages of Spray-Up Technology
Spray-Up is increasingly favored due to its effective combination of production efficiency and product quality. Key advantages include:
- Superior production speed
Semi-automated processes significantly boost productivity, making it ideal for large production orders. - Optimized labor costs
Reduced dependency on manual skills helps save operational costs and stabilize output quality. - Design flexibility
Suitable for curved, angular, or asymmetrical products. Easily creates various sizes and complex structures within the same system. - High durability and corrosion resistance
Finished products have excellent mechanical properties, smooth surfaces, and can withstand chemicals and harsh environments—ideal for the marine, construction, and industrial sectors.
5. Applications of Spray-Up Technology
Thanks to its flexibility and ability to produce complex products, Spray-Up technology is widely applied across many modern industries:
- Marine industry
Ideal for manufacturing composite hulls, boats, and canoes—reducing weight, saving fuel, and increasing corrosion resistance in harsh seawater environments. - Construction industry
Used to create domes, panels, water, and chemical storage tanks—offering excellent strength, lightweight properties, and weather resistance for outdoor or damp environments. - Transportation industry
Applied in making bus bodies, automotive parts, and train components—requiring lightweight, sturdy structures with high aesthetic finishes, contributing to fuel efficiency. - Heavy and chemical industries
Enables the production of industrial tanks, chemical pipelines, chimneys, and more, providing outstanding chemical resistance, extending equipment life, and reducing maintenance costs.
6. Limitations of Spray-Up Technology and Solutions
Despite many outstanding advantages, Spray-Up technology still has certain limitations. However, with appropriate technical measures, these weaknesses can be effectively managed:
- Inconsistent fiber-resin ratio
- Problem: Inaccurate spraying can cause imbalance between reinforcement fibers and resin, affecting strength and quality.
- Solution: Properly train technicians and equip modern spray guns with automatic flow adjustments to ensure uniform mixing during spraying.
- Problem: Inaccurate spraying can cause imbalance between reinforcement fibers and resin, affecting strength and quality.
- Difficulty controlling material thickness
- Problem: Compared to technologies like RTM, Spray-Up offers lower precision in thickness control, leading to uneven layers.
- Solution: Use specialized rollers to even out the surface after spraying, adjusting thickness and eliminating air bubbles to stabilize product quality.
- Problem: Compared to technologies like RTM, Spray-Up offers lower precision in thickness control, leading to uneven layers.
- Lower mechanical strength compared to Pultrusion or LRTM
- Problem: Spray Up is not suitable for components requiring heavy load-bearing capacity.
- Solution: Use Spray Up for non-load-bearing parts, or combine it with other technologies like LRTM to optimize performance for higher demands.
- Problem: Spray Up is not suitable for components requiring heavy load-bearing capacity.
7. Conclusion – Is Spray-Up the Best Solution for Composites?
Spray-Up may not be the “one-size-fits-all” technology for every composite product, but it is an optimal solution when balancing design flexibility, production speed, and cost efficiency. Its ability to form complex parts makes trusted for mass production needs.
At THE FRONT, we proudly apply advanced this technology combined with strict quality control systems to create internationally standardized composite products—meeting the rigorous demands across industries such as construction, marine, transportation, and heavy industry.
This technology is not just a production method; it is a practical solution for businesses seeking a balance between quality, efficiency, and cost.
THE FRONT JSC
Address: Block H19, St. N1, Nam Thuan Industrial Park, Duc Hoa Dong Ward, Duc Hoa District, Long An Province
Hotline: +(84)96-888-7363
Email: [email protected]