Choosing the right grating for your project is crucial, whether you’re working in industrial facilities, marine environments, or commercial construction. Two of the most popular options available are FRP (Fiber Reinforced Plastic) grating, also known as GRP (Glass Reinforced Plastic) grating, and traditional steel grating. Both materials have unique strengths and benefits, but which one is better for your needs?
This guide will walk you through the key differences, advantages, and potential drawbacks of FRP grating and steel grating, helping you make an informed decision based on your project requirements.
What Is FRP Grating?
FRP grating is a composite material made from fiberglass reinforcement and a resin matrix, typically polyester or vinyl ester resin. The combination of fiberglass and resin results in a grating that is lightweight, strong, and highly resistant to corrosion, making it ideal for industrial, marine, and commercial applications where traditional metals may fail.
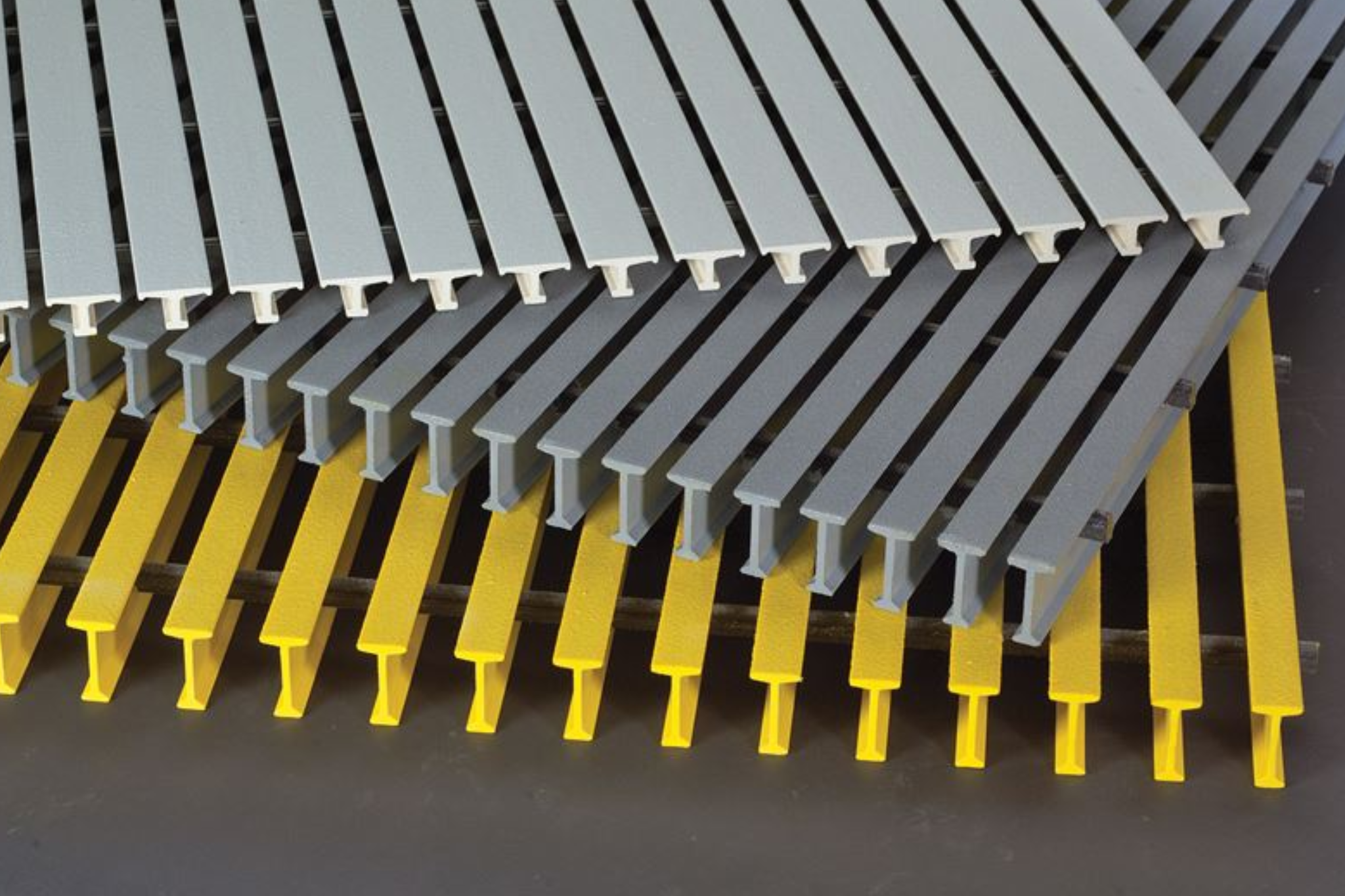
What Is Steel Grating?
Steel grating, on the other hand, is typically made from welded or pressed steel bars. Known for its strength and load-bearing capacity, steel grating has been a standard choice in industrial settings for decades. It is often coated with galvanized or stainless steel finishes to enhance corrosion resistance and withstand heavy use, especially in environments requiring high durability.
Key Comparisons: FRP Grating vs. Steel Grating
Let’s take a closer look at the main factors to consider when choosing between FRP grating and steel grating.
1. Corrosion Resistance
- FRP Grating: One of the biggest advantages of FRP grating is its superior corrosion resistance. FRP grating does not rust, corrode, or degrade when exposed to harsh chemicals, saltwater, or moisture. This makes it an excellent choice for environments where exposure to corrosive substances is common, such as chemical plants, offshore oil rigs, and wastewater treatment facilities.
- Steel Grating: Steel grating can be treated with a galvanized or stainless steel coating to improve corrosion resistance, but it is still susceptible to rust and degradation over time, especially when exposed to harsh chemicals, saltwater, or humid environments. This means steel grating may require more frequent maintenance and replacements in corrosive settings.
Note: FRP grating is the clear winner for environments that involve moisture, chemicals, or saltwater, as it is far more resistant to corrosion.
2. Strength and Load-Bearing Capacity
- FRP Grating: While FRP grating is strong and suitable for many load-bearing applications, it is generally less robust than steel when it comes to handling extremely heavy loads. However, FRP grating’s unique strength-to-weight ratio allows it to perform well in many industrial applications where the load requirements are moderate to heavy.
- Steel Grating: Steel grating is known for its high load-bearing capacity, making it the preferred choice for applications that require the grating to withstand significant weight, such as in heavy machinery areas, truck ramps, and other industrial environments with heavy foot or vehicle traffic.
Note: Steel grating wins in terms of load-bearing capacity, making it the better choice for projects with extremely high weight requirements. However, FRP grating is still a strong contender for many standard load-bearing applications.
3. Weight and Ease of Installation
- FRP Grating: FRP grating is approximately 70% lighter than steel grating, which makes it much easier to transport, handle, and install. This reduction in weight can lead to lower transportation and installation costs, as well as a reduced need for heavy lifting equipment. The lightweight nature of FRP grating also makes it easier to cut and customize on-site with simple tools.
- Steel Grating: Steel grating is significantly heavier than FRP grating, which can complicate transportation and installation. Heavy equipment is often required to move and install steel grating, adding to the labor costs and installation time. Cutting and customizing steel grating also require specialized tools, which can increase both time and expenses.
Note: FRP grating is the winner in terms of weight, ease of handling, and installation, making it a practical choice for projects that prioritize efficiency and cost savings during installation.
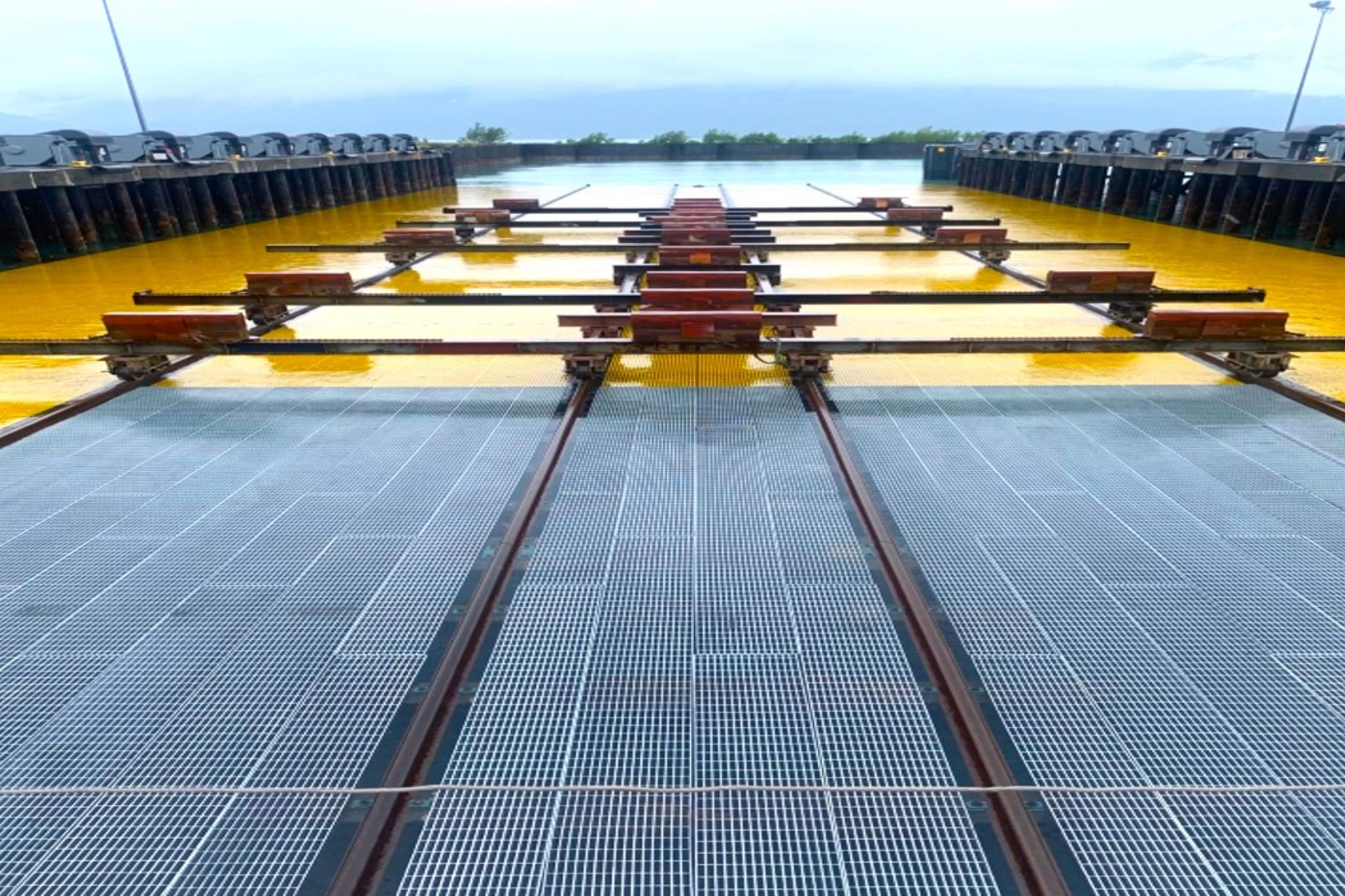
4. Safety and Non-Slip Properties
- FRP Grating: FRP grating can be manufactured with a non-slip surface, which makes it highly suitable for areas exposed to moisture, oils, or chemicals. Its non-slip surface improves workplace safety by reducing the risk of slips and falls. Additionally, FRP is non-conductive, providing an extra layer of safety in environments where electrical conductivity is a concern.
- Steel Grating: Steel grating can also be made with non-slip coatings or serrated surfaces, but over time, exposure to moisture and wear can reduce its slip resistance. Steel is also conductive, which may be a safety concern in environments where exposure to electrical currents is possible.
Note: FRP grating takes the lead for safety, particularly in wet or electrically sensitive areas, due to its non-slip properties and non-conductive nature.
5. Maintenance and Longevity
- FRP Grating: FRP grating is highly resistant to corrosion, UV rays, and harsh chemicals, which means it requires minimal maintenance and is extremely durable. It does not need protective coatings, and the color and surface integrity are retained for many years. The low maintenance requirements contribute to FRP grating’s overall cost-effectiveness.
- Steel Grating: Steel grating requires more frequent maintenance to prevent rust and corrosion, especially in environments exposed to moisture or chemicals. Galvanized or stainless steel finishes help to improve its durability, but over time, maintenance such as repainting, recoating, or replacing sections may be necessary.
Note: FRP grating wins in terms of maintenance and longevity, as it is designed to withstand corrosive environments and harsh conditions without frequent upkeep.
6. Cost Efficiency
- FRP Grating: While the initial cost of FRP grating may be higher than that of untreated steel, the savings on maintenance, replacement, and labor often make it more cost-effective in the long run. Additionally, FRP grating’s lightweight nature reduces installation and transportation costs, adding to its overall value.
- Steel Grating: Steel grating may be more affordable upfront, particularly if it’s not galvanized or stainless steel. However, the ongoing costs associated with maintenance, repairs, and possible replacements can add up over time, especially in corrosive environments.
Note: FRP grating offers better long-term cost efficiency, especially in environments where maintenance would be frequent for steel grating.
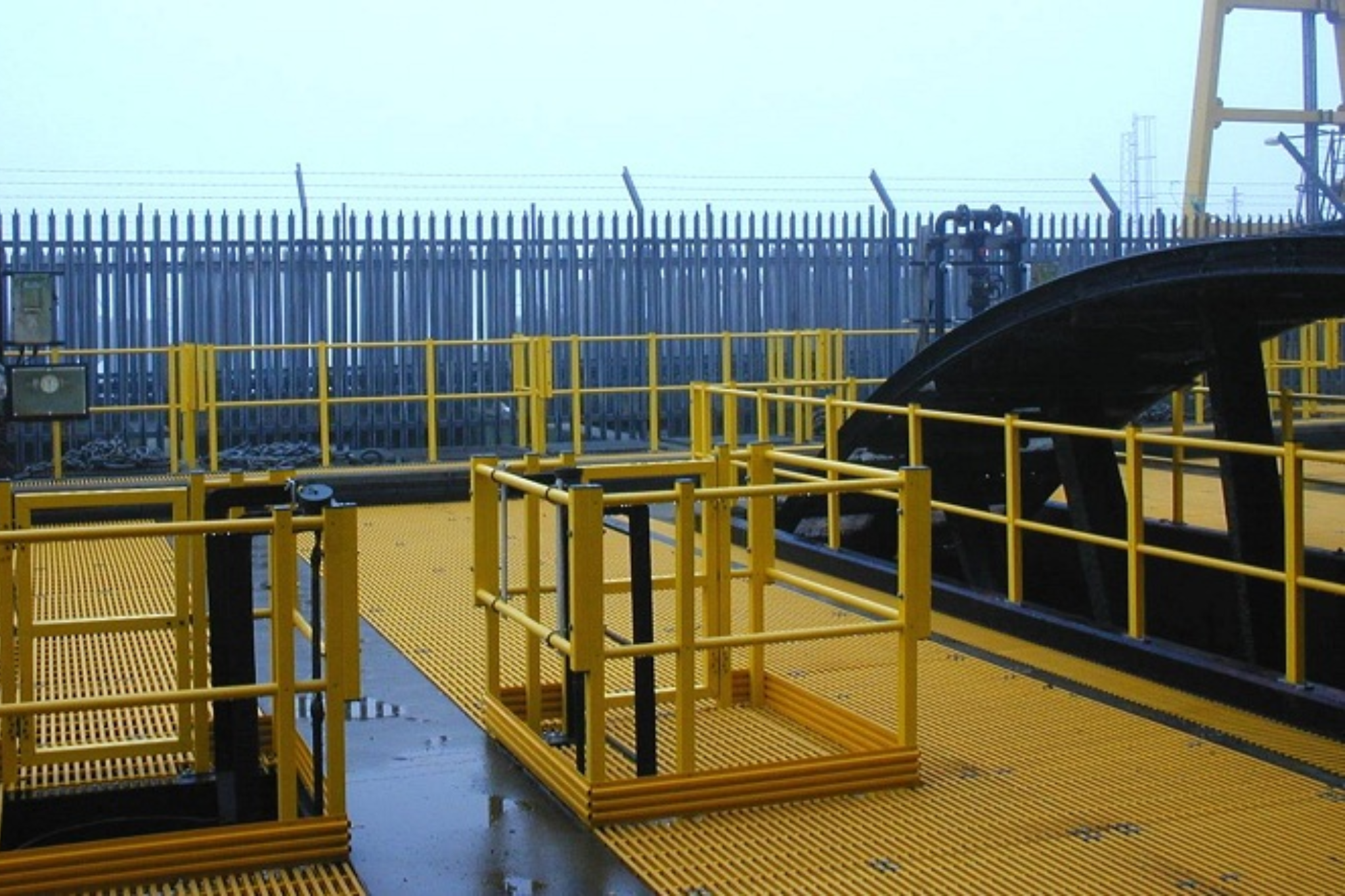
Making the Right Choice for Your Project
When deciding between FRP grating and steel grating, consider the specific demands of your project:
- Choose FRP Grating if you’re looking for a lightweight, corrosion-resistant, and low-maintenance option, especially for applications exposed to moisture, chemicals, or electrical hazards. FRP grating offers excellent long-term cost efficiency and safety, making it a smart choice for many industrial, marine, and commercial applications.
- Choose Steel Grating if you need maximum load-bearing capacity and are working in environments where high strength is essential. Steel grating is often preferred in heavy industrial settings where the primary concern is withstanding significant weight.
By understanding the strengths and limitations of each type, you can make an informed choice that aligns with your project’s needs and priorities. Whether you choose FRP or steel grating, selecting the right material will enhance the durability, safety, and efficiency of your project.