FRP chemical tanks are crucial in industries requiring safe, long-lasting, and resistant storage solutions for hazardous chemicals. These tanks are composed of Fiberglass Reinforced Plastic (FRP), a composite material known for its excellent strength, lightweight nature, and corrosion resistance. However, the effectiveness of an FRP chemical tank largely depends on the materials used in its construction, particularly the type of resin and fiberglass chosen for the tank’s specific application. In this article, we’ll explore the best materials for FRP chemical tanks, and explain why these tanks are ideal for storing corrosive and hazardous chemicals.
What Are FRP Chemical Tanks?
FRP chemical tanks are specialized storage containers made from a composite material of glass fibers embedded in a resin matrix, typically used in industrial environments where chemical storage is required. They are designed to resist corrosion and chemical degradation, which can compromise the structural integrity of tanks made from metals or traditional plastics.
Why Material Selection Matters for FRP Chemical Tanks
The materials chosen for FRP chemical tanks are critical to their performance, longevity, and safety. Tanks must be designed with the correct resin system and fiberglass reinforcement to ensure compatibility with the chemicals being stored. Poor material choices can result in leaks, tank failure, or contamination of stored substances.
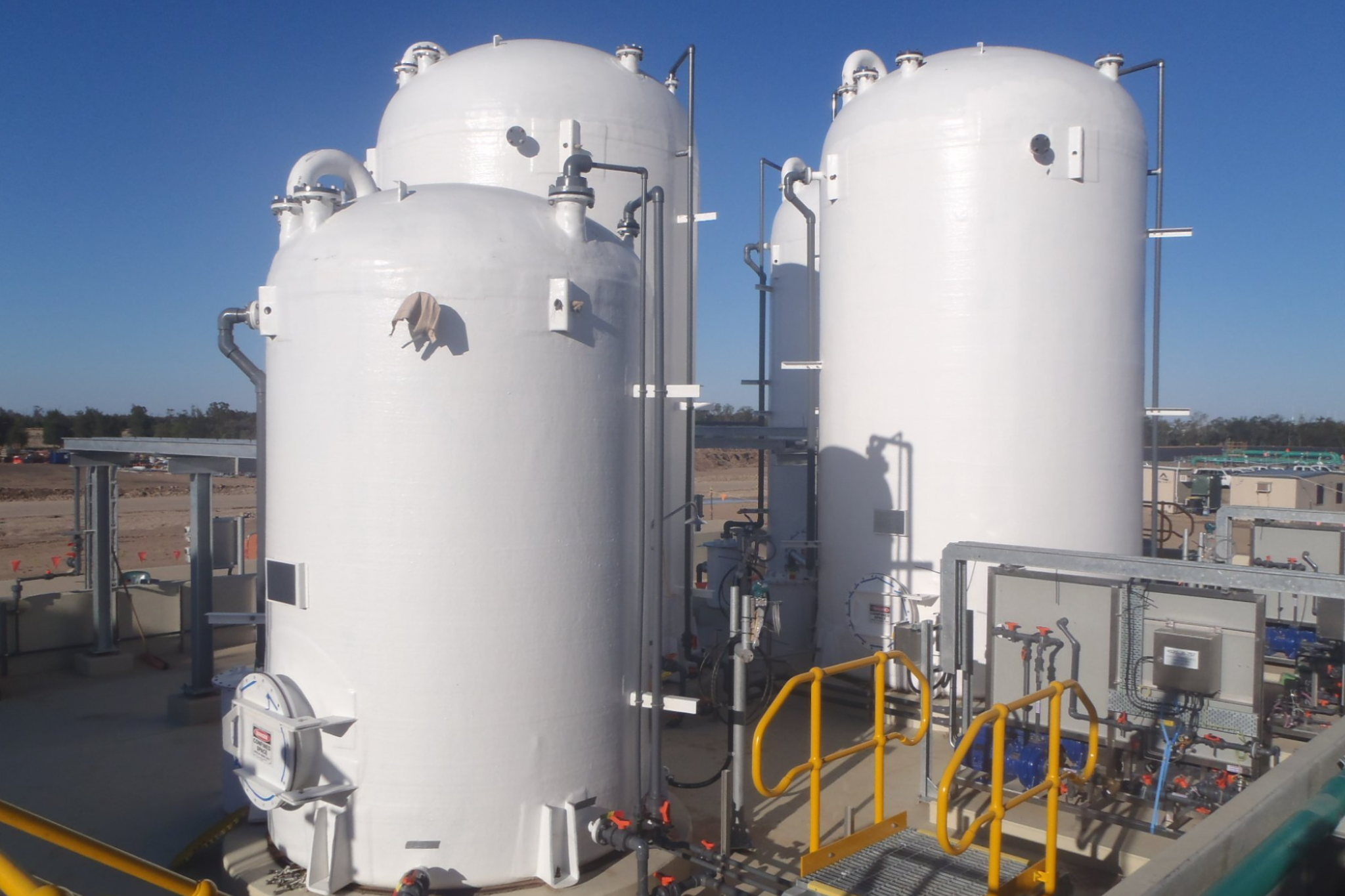
Best Materials for FRP Chemical Tanks
1. Resin Selection
The resin used in the tank’s matrix plays a vital role in determining its chemical resistance. Here are some of the most commonly used resins for FRP chemical tanks:
- Vinyl Ester Resin
- Why It’s Best for Chemical Tanks: Vinyl ester resins are highly resistant to a wide range of chemicals, including strong acids, alkalis, and solvents. They also have excellent resistance to heat, making them an ideal choice for industries like chemical processing, wastewater treatment, and petrochemical storage. Vinyl ester resins are particularly beneficial for FRP tanks exposed to aggressive or corrosive chemicals, offering a long service life without degradation.
- Applications: These resins are commonly used in tanks that store highly corrosive substances like sulfuric acid, hydrochloric acid, or caustic soda.
- Epoxy Resin
- Why It’s Best for Chemical Tanks: Epoxy resins are known for their superior mechanical properties and exceptional chemical resistance. They are less permeable than other resin types, offering higher durability and enhanced resistance to water and solvents. While epoxy resins are more expensive, they provide a premium solution for storing volatile chemicals or in environments where chemical tanks are exposed to significant stress or pressure.
- Applications: Epoxy resins are ideal for industries handling hazardous waste, fuels, or sensitive chemicals requiring safe, stable storage conditions.
- Polyester Resin
- Why It’s Best for Chemical Tanks: Polyester resins are the most cost-effective option for FRP chemical tanks, offering a good balance between chemical resistance and affordability. Although not as chemically resistant as vinyl ester or epoxy, polyester resins can still handle moderately corrosive substances like water, sewage, and certain chemicals.
- Applications: Polyester resins are commonly used in non-critical chemical storage, where the stored materials do not pose significant risks of corrosion, such as wastewater or water treatment tanks.
2. Fiberglass Reinforcement
The strength and structural integrity of an FRP chemical tank are largely determined by the type of fiberglass reinforcement used. There are different types of fiberglass reinforcements, each offering specific advantages for chemical tank construction.
- E-Glass
- Why It’s Best for Chemical Tanks: E-glass, or electrical-grade glass, is the most commonly used fiberglass in FRP tanks. It offers good chemical resistance and mechanical strength, making it a versatile choice for a wide range of chemical storage applications. E-glass also provides excellent electrical insulation and is resistant to moisture, making it suitable for general-purpose tanks.
- Applications: E-glass is often used in tanks that store less aggressive chemicals or in environments where moderate durability is required.
- C-Glass
- Why It’s Best for Chemical Tanks: C-glass, or chemical-grade glass, is specially formulated for superior corrosion resistance in highly acidic environments. This type of fiberglass is commonly used in tanks that store strong acids or other highly corrosive chemicals.
- Applications: C-glass is the material of choice for FRP chemical tanks used in environments where acid exposure is constant, such as chemical manufacturing plants and processing facilities.
- S-Glass
- Why It’s Best for Chemical Tanks: S-glass is a high-performance fiberglass known for its high tensile strength and exceptional resistance to impact and wear. While more expensive than E-glass and C-glass, S-glass is used when tanks need to withstand significant mechanical stress or when extra durability is needed.
- Applications: S-glass is often used in tanks that store volatile chemicals or in environments where the tank may be subject to mechanical damage.
Why FRP Chemical Tanks Are Ideal for Chemical Storage
FRP chemical tanks offer several key advantages that make them ideal for storing hazardous chemicals. Here’s why these tanks are preferred by many industries:
1. Corrosion Resistance
The materials used in FRP chemical tanks, such as vinyl ester or epoxy resin, provide superior resistance to corrosive chemicals, preventing tank failure and ensuring the safety of stored materials.
2. Lightweight Yet Strong
Compared to metal tanks, FRP tanks are much lighter while maintaining exceptional strength. This makes them easier to transport, install, and maintain, reducing overall costs and logistical challenges for companies that need large storage solutions.
3. Customizable
FRP tanks can be easily customized to meet specific storage requirements. The flexibility in material selection (resin and fiberglass types) allows tank manufacturers to tailor tanks to different chemicals and environmental conditions, ensuring optimal safety and performance.
4. Long Lifespan
Due to their high resistance to chemical degradation, FRP tanks last significantly longer than other types of storage tanks. This durability translates into fewer repairs, less maintenance, and lower costs over the lifespan of the tank.
Conclusion
When choosing the best materials for FRP chemical tanks, the selection of the right resin and fiberglass reinforcement is crucial to ensure the tank’s performance and safety. Vinyl ester, epoxy, and polyester resins each offer specific advantages depending on the chemical being stored, while fiberglass options like E-glass, C-glass, and S-glass provide varying levels of strength and corrosion resistance.
FRP chemical tanks have become the go-to solution for industries requiring safe, durable, and customizable storage solutions for hazardous and corrosive chemicals. By selecting the right materials, companies can ensure that their storage tanks will provide long-term protection and peace of mind.
For businesses seeking a reliable chemical storage solution, FRP chemical tanks represent the best combination of strength, corrosion resistance, and cost-effectiveness.