Pultrusion is one of the most efficient and precise technologies in the composite materials industry today. It enables the continuous production of high-strength, lightweight profiles with superior dimensional stability — all at industrial scale
1. Introduction to Pultrusion Technology
What is Pultrusion?
Pultrusion is a manufacturing process for composite materials, where continuous strands of reinforcing fibers (such as fiberglass, carbon fiber, etc.) are pulled through a resin bath and a heated die, then cured and cut to the desired lengths. The term “Pultrusion” combines “pull” and “extrusion,” reflecting the continuous pulling characteristic of the process.
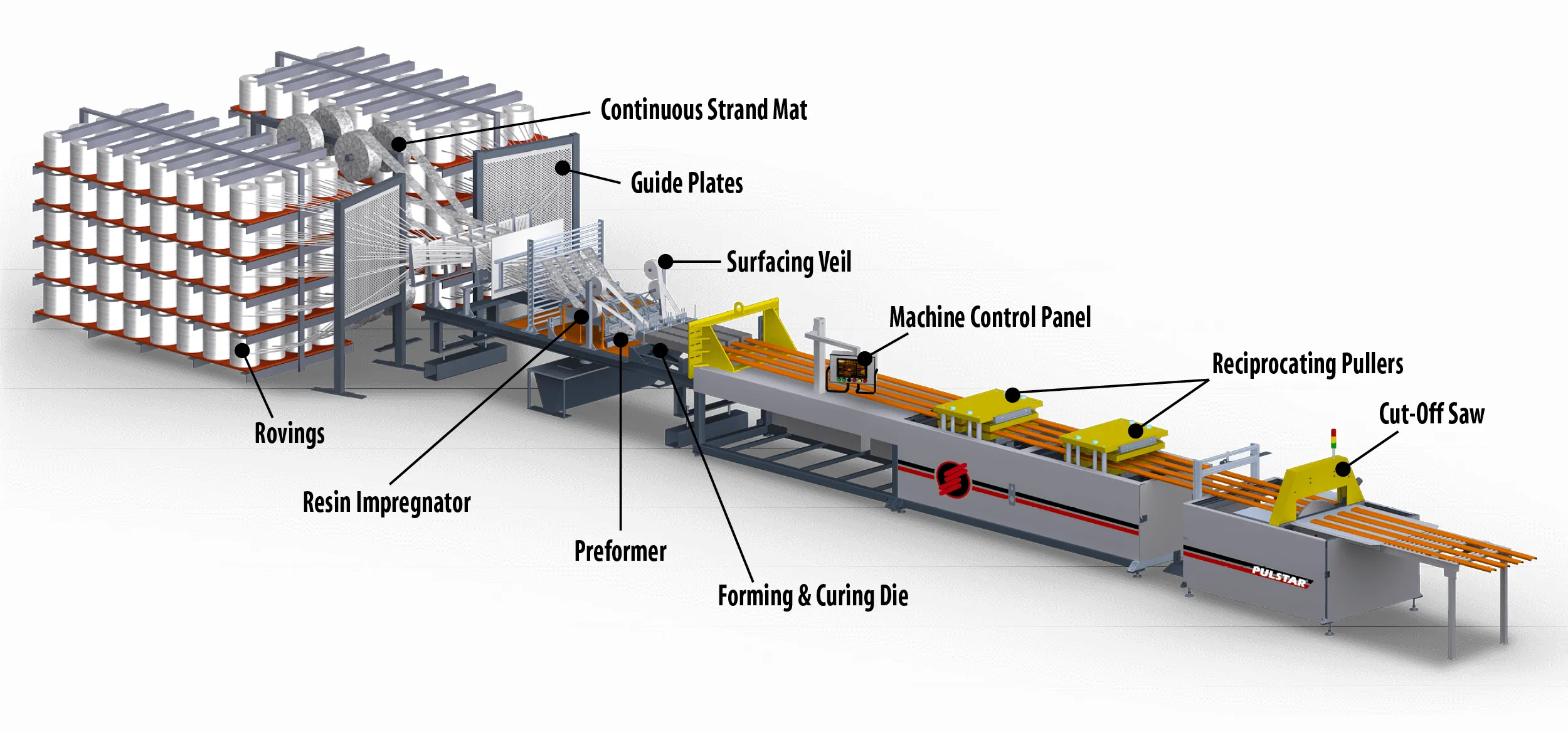
The History and Development of Pultrusion Technology
First developed in the 1950s in the United States, Pultrusion quickly established itself as one of the most efficient and advanced methods for producing composite materials. With its ability to deliver high precision, outstanding stability, and continuous production efficiency, Pultrusion has undergone constant improvements. Today, it is widely adopted across numerous industries worldwide.
2. How Pultrusion Works
The Pultrusion process operates continuously and automatically through three main stages:
Resin Impregnation of Reinforcement Fibers
Reinforcement fibers (such as fiberglass, carbon fiber, or aramid) are continuously pulled through a liquid resin bath — typically Polyester, Vinylester, or Epoxy — ensuring thorough impregnation and optimal bonding between fibers and the resin matrix.
Shaping and Curing in a Heated Die
After resin impregnation, the fibers are pulled through a fixed-shape die. Here, the system applies heat to cure the resin, forming a composite product with precise shape and high durability.
Cutting to Desired Lengths
Finally, the cured composite is continuously pulled out of the die and cut to standard or customized lengths, ready for various industrial applications.
3. Pultrusion Composite Manufacturing Process
Pultrusion follows a closed-loop, highly automated, continuous production system comprising the following steps:
Step 1: Preparation of Reinforcement Fibers
Fibers such as fiberglass, carbon fiber, or aramid are loaded into the system. These fibers serve as the primary load-bearing components of the composite product.
Step 2: Resin Impregnation
Fibers are continuously drawn through a bath of liquid resin — Polyester, Vinylester, or Epoxy — depending on technical requirements and the desired mechanical properties.
Step 3: Pulling Through the Shaping Die
Post impregnation, the fibers are guided into a shaping die designed according to the cross-section of the final product. The pulling mechanism ensures a stable speed, maintaining consistent fiber-resin movement through the die.
Step 4: Heating and Curing
Inside the die, precise heat control initiates the curing process, fixing the product’s shape while enhancing its hardness, strength, and stability.
Step 5: Cutting the Finished Product
After exiting the die, the composite material is cut using specialized blades or automatic cutters to standard or customized lengths, ready for practical applications.
4. Advantages of Pultrusion Technology
Pultrusion offers numerous outstanding advantages over traditional composite manufacturing methods:
High Automation
The fully automated process minimizes labor needs and optimizes costs, making it ideal for large-scale, stable production.
Uniform Product Quality
Products have smooth surfaces, minimal technical errors, and virtually no air bubbles, ensuring aesthetic appeal and reliability.
Superior Mechanical Strength
Pultruded products exhibit high tensile strength and excellent flexural and compressive resistance, suitable for demanding structural applications.
Outstanding Production Efficiency
Continuous, fast production significantly boosts output compared to traditional manual or semi-automatic methods.
5. Applications of Pultrusion in Industry
Thanks to superior mechanical properties, corrosion resistance, and lightweight characteristics, Pultrusion is widely applied across various industries:
Construction Industry
Manufacturing FRP rebar for fiber-reinforced concrete, insulation panels, bridge beams, composite roof trusses, and custom-shaped structural components.
Transportation Sector
Producing bridge guardrails, safety barriers, vehicle restraint posts, signpost supports, and components requiring high durability and weather resistance.
Electrical Industry
Supplying cable trays, insulation panels, busbar support profiles, composite utility poles, and other insulating components for harsh environments.
Marine Industry
Used in ship hulls, decks, railings, and corrosion-resistant components, especially effective in humid, salty maritime environments.
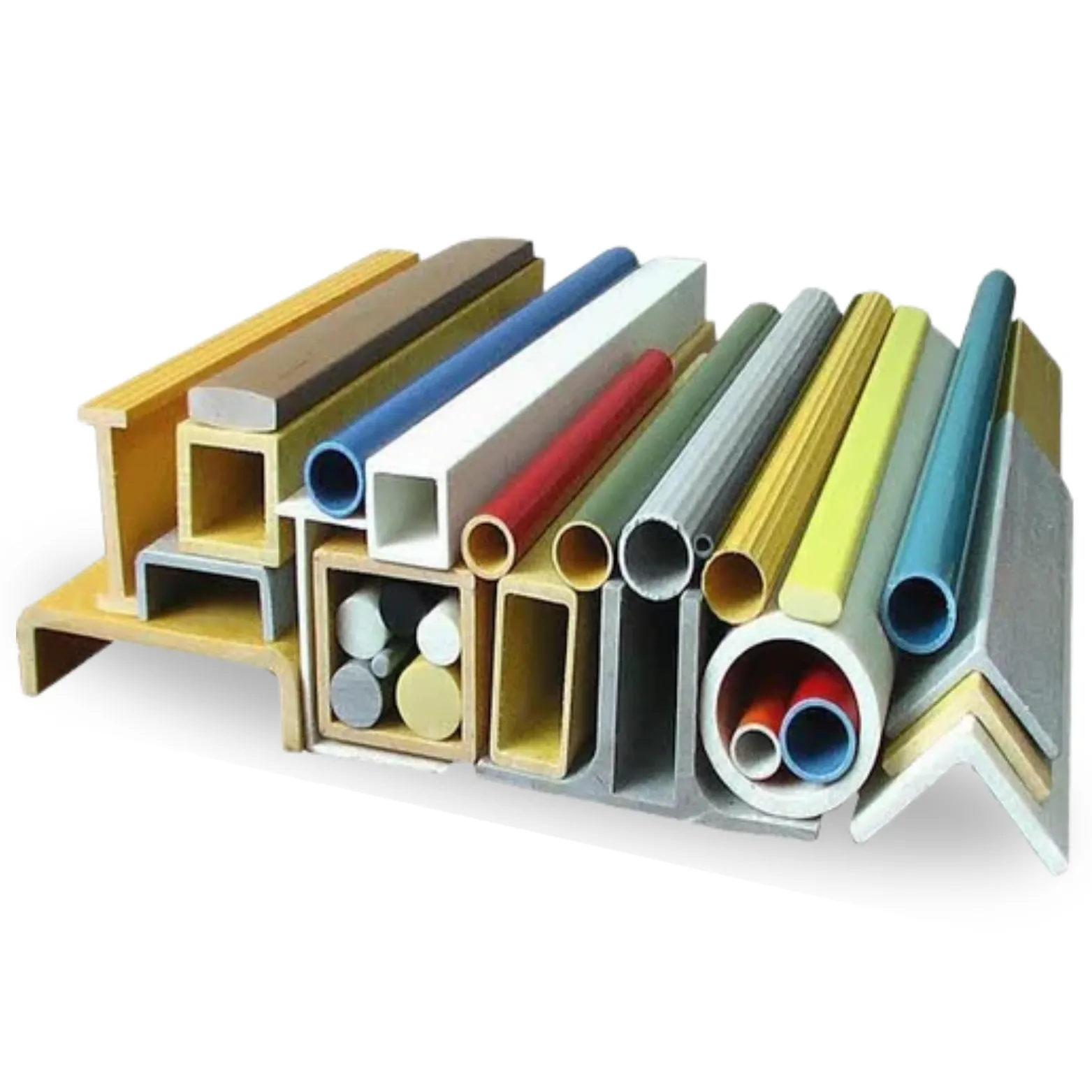
6. Why Pultrusion is Favored in Composite Manufacturing
Pultrusion technology is increasingly chosen by manufacturers due to its technical and economic advantages:
Production of Long, Continuous Profiles
The continuous pulling process enables manufacturing components of unlimited length, ideal for beams, rods, pipes, and guide rails.
Lightweight with High Strength
Pultruded composites are up to 70% lighter than metals, while maintaining excellent tensile, bending, and compressive strength.
Excellent Corrosion Resistance
Products resist rust and endure harsh conditions like seawater, industrial chemicals, and humid climates — ideal for maritime, chemical, and outdoor infrastructure industries.
Optimized Production Costs
Compared to materials like stainless steel or extruded aluminum, Pultrusion offers lower raw material and operating costs and reduces maintenance expenses throughout the product lifecycle.
7. Conclusion – Pultrusion as the Future of Composite Materials
In an era of globalization and sustainable development, industries increasingly demand lightweight, durable, and eco-friendly materials. Pultrusion technology stands out as a pioneering solution that fully meets these needs — effectively replacing traditional metals with modern, high-performance composites.
With continuous production capabilities, customizable designs, and OEM scalability, Pultrusion is paving the way for a new era in material manufacturing. It is not merely a technical solution but a long-term growth strategy for forward-thinking enterprises.
At THE FRONT, we embrace Pultrusion not only as a technology, but as a strategic direction. By applying world-class composite manufacturing standards and continuously investing in tooling and material science, we are committed to delivering tailor-made, performance-driven solutions for global clients — from infrastructure to advanced industrial applications.
THE FRONT JSC
Address: Block H19, St. N1, Nam Thuan Industrial Park, Duc Hoa Dong Ward, Duc Hoa District, Long An Province
Hotline: +(84)96-888-7363
Email: [email protected]